ABOUT KEY Precision
Our engineering division stands as a testament to our dedication to exacting standards. Through precision mould design and manufacturing, we aim to lead the industry in crafting intricate components, pushing the boundaries of what is possible, and consistently delivering products that embody the highest levels of quality and accuracy.
From Concept to Design, DFM to Prototyping, and full validation and mass production, Key Precision is a proven trusted manufacturing partner.
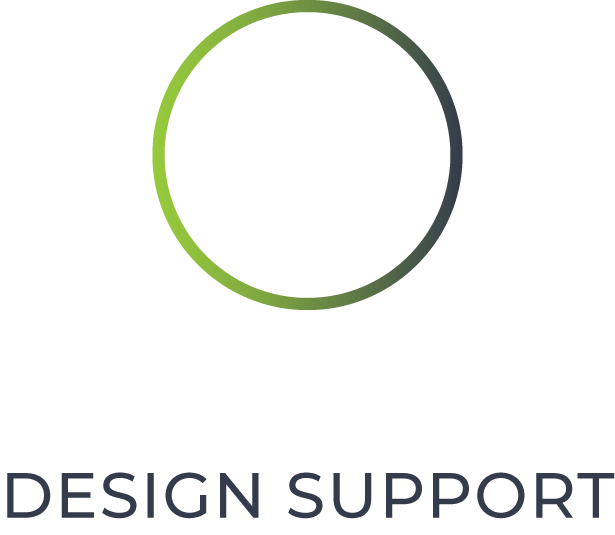
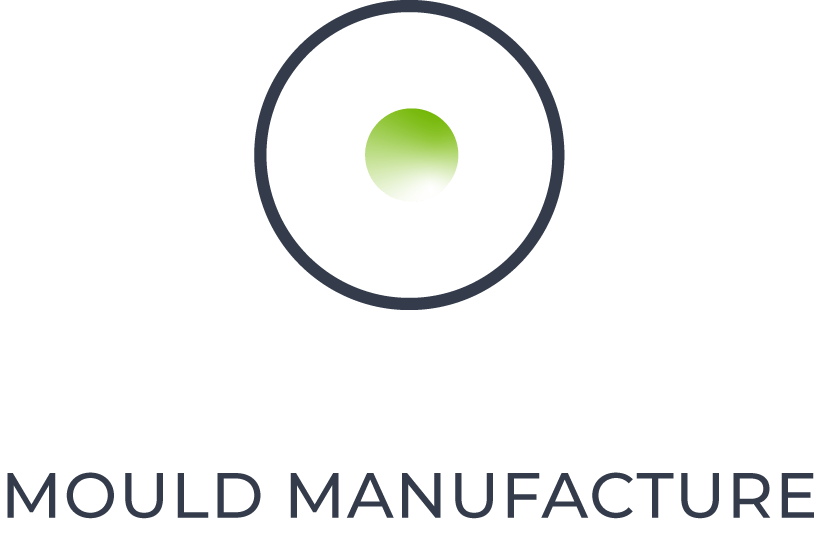
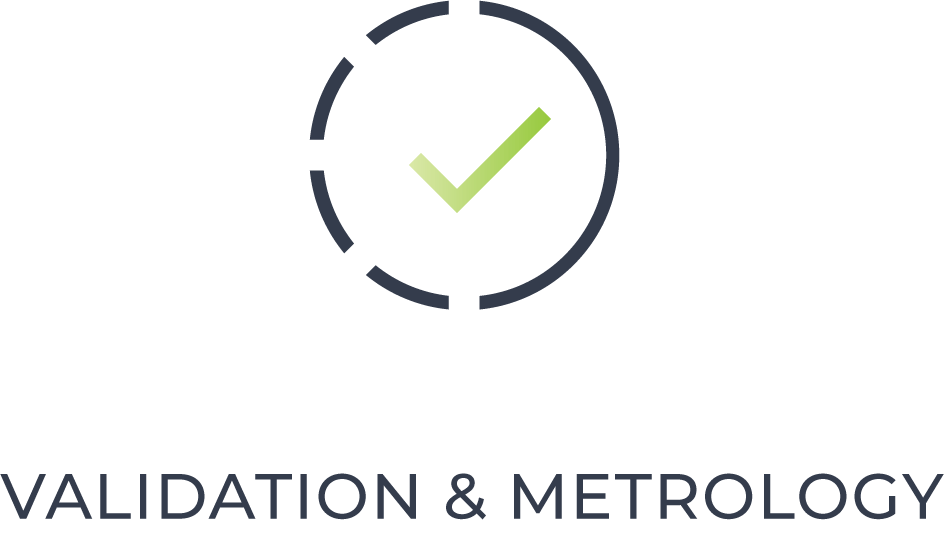
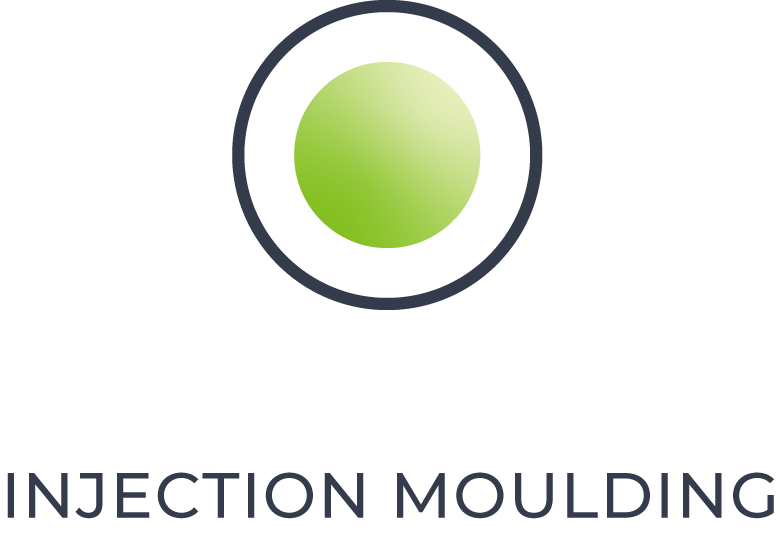
- Mould Service & Repair
- Design for Manufacture
- Mould Design & Manufacture
- Metrology Services
- Precision Engineering

Mould Service & Repair
Declan and his team of highly skilled toolmakers are here to help. Offering a daily collection and delivery service our team are here to ensure a fast and efficient turnaround of your mould repairs and modification.
Certified to ISO 13485 and AS9100 Key Precision can offer you:
- Laser Welding
- EDM
- Wire Erosion
- CNC Machining
- DFM support
- Collection & Delivery Service
- Mould Trialling Service
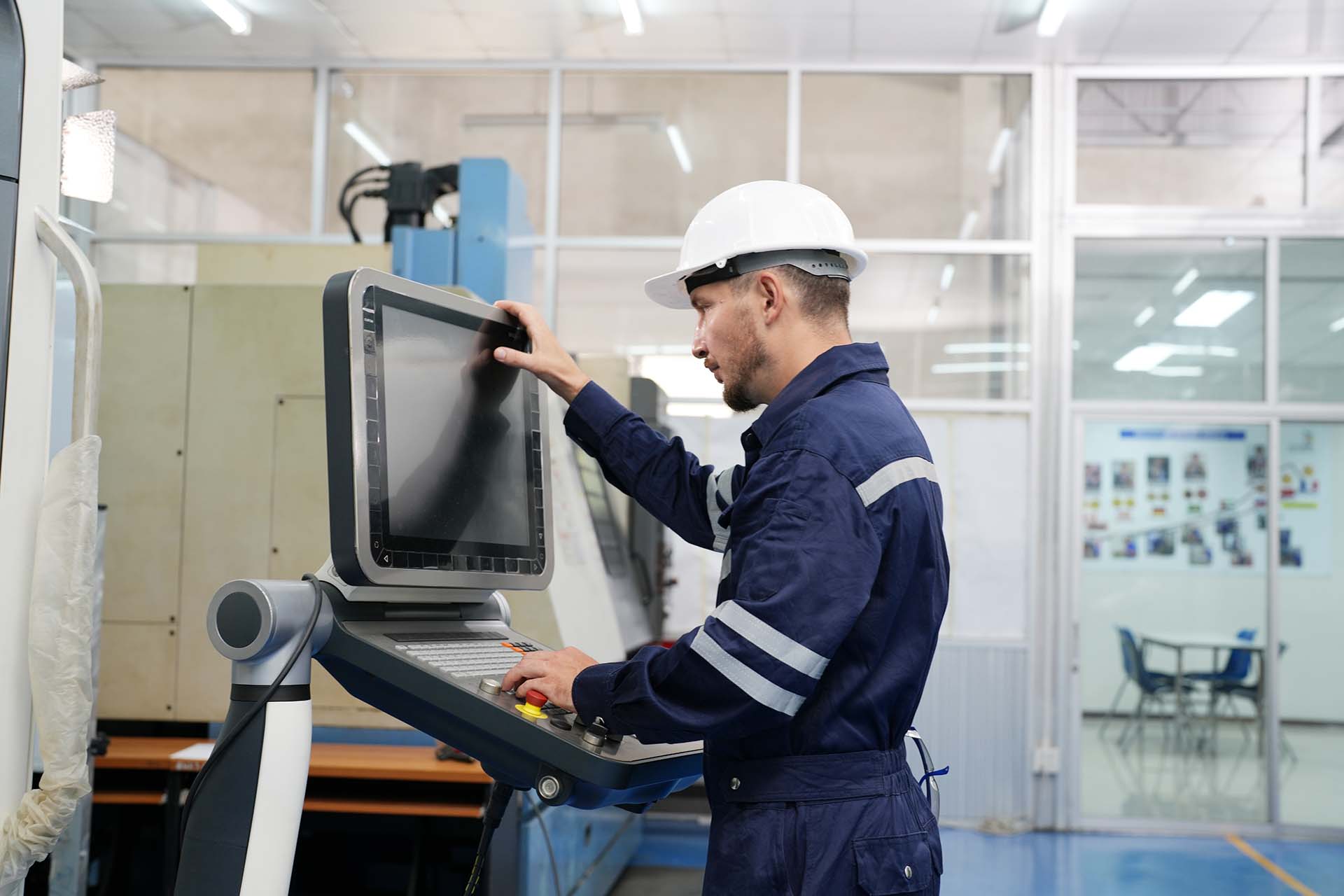
Product Design & Design for Manufacturing (DFM)
In the realm of contract injection moulding, product design and Design for Manufacture (DFM) are pivotal stages that dictate the efficiency, quality, and cost-effectiveness of the entire manufacturing process. As contract manufacturers, our expertise lies in seamlessly translating our clients’ conceptual designs into manufacturable products that meet their precise specifications and requirements.
Product design serves as the foundation of the manufacturing journey, where intricate details and functional requirements are crafted into a tangible blueprint. Through collaborative engagement with our clients, we use our expertise in injection moulding to optimise designs for manufacturability, ensuring that each component is tailored to withstand the rigors of the production process while maximising efficiency and minimising material waste.
Design for Manufacture (DFM) combines creative ideas with practical manufacturing needs. It’s about designing products in a way that considers how they will be made. At Key our team of seasoned engineers meticulously evaluates each design iteration, identifying opportunities for streamlining production processes, minimising tooling costs, and enhancing part performance. Utilising advanced CAD/CAM software and simulation tools, we validate designs in virtual environments, exploring and addressing potential manufacturing challenges and optimising part geometry for injection moulding.
The critical relationship between product design and Design for Manufacture (DFM) is fundamental to our commitment to delivering exceptional value and innovation to our clients. Through proactive collaboration, design refinement, and rigorous validation, we empower our clients to bring their concepts to life with precision, efficiency, and cost-effectiveness.
As trusted partners in contract injection moulding, we stand ready to collaborate with you at every stage of the product development journey, from initial design conception to final production, ensuring that your vision is realised with unparalleled quality and reliability.
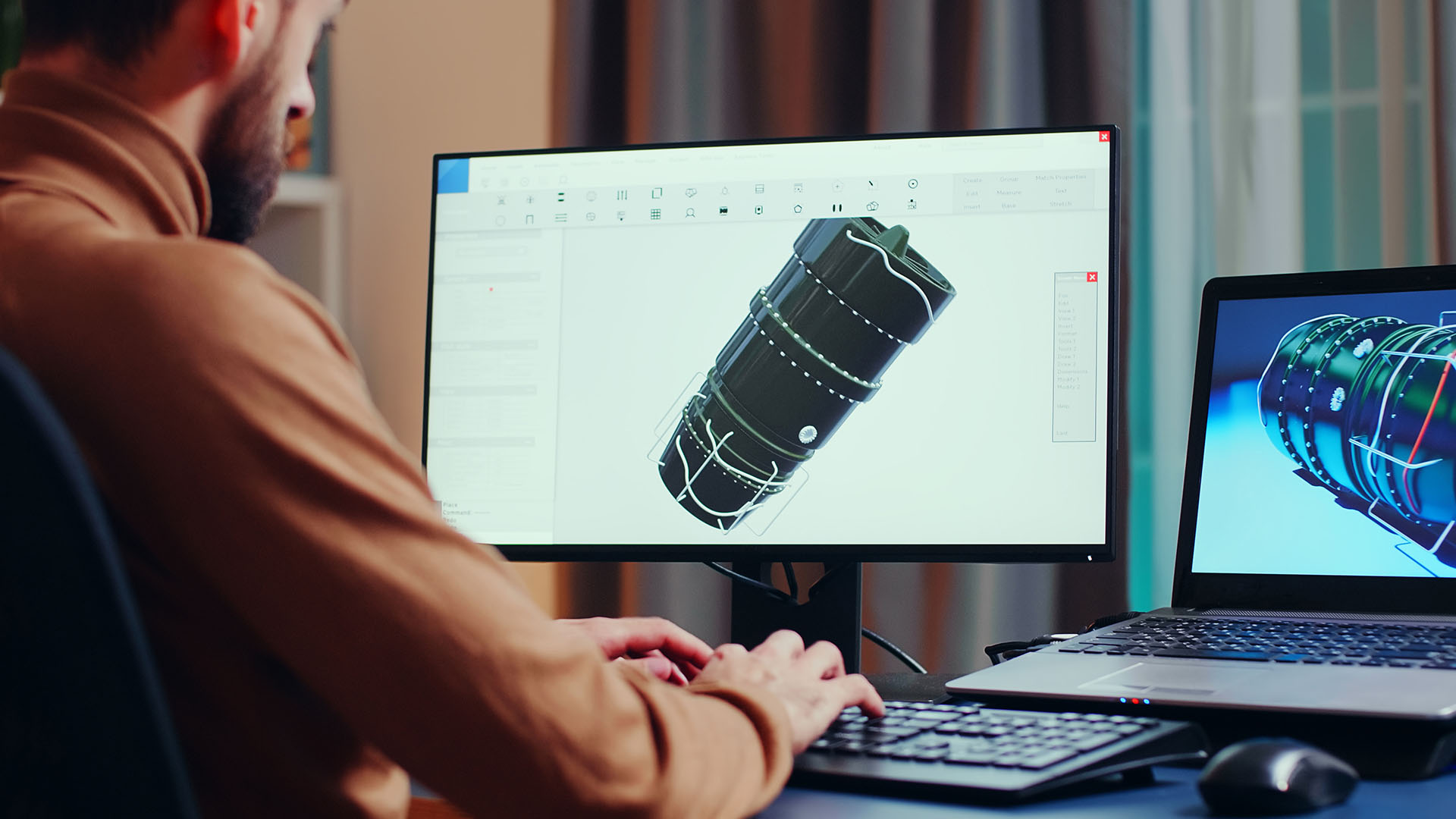
Mould Design & Manufacture
At Key Precision we can offer our customers a premium mould manufacturing services, where precision meets innovation to bring your designs to life. With decades of experience and a team of master mould makers, we specialize in delivering high-quality moulds tailored to your exact specifications.
At our state-of-the-art facility, we leverage advanced precision machining techniques such as EDM, wire erosion, milling, and turning to create moulds with unparalleled accuracy and consistency. Our in-house capabilities, combined with strategic partnerships with external approved partners, ensure that we have the flexibility and expertise to handle projects of any complexity or scale.
From prototyping to production, our dedicated engineers work closely with you every step of the way to ensure that your moulds are manufactured to the highest standards of quality and precision.
Partner with us for your mould manufacturing needs and experience the difference that our commitment to excellence and many years of industry experience can make.
Contact us today to learn more about our capabilities and how we can help bring your vision to reality with precision-crafted moulds that exceed your expectations.
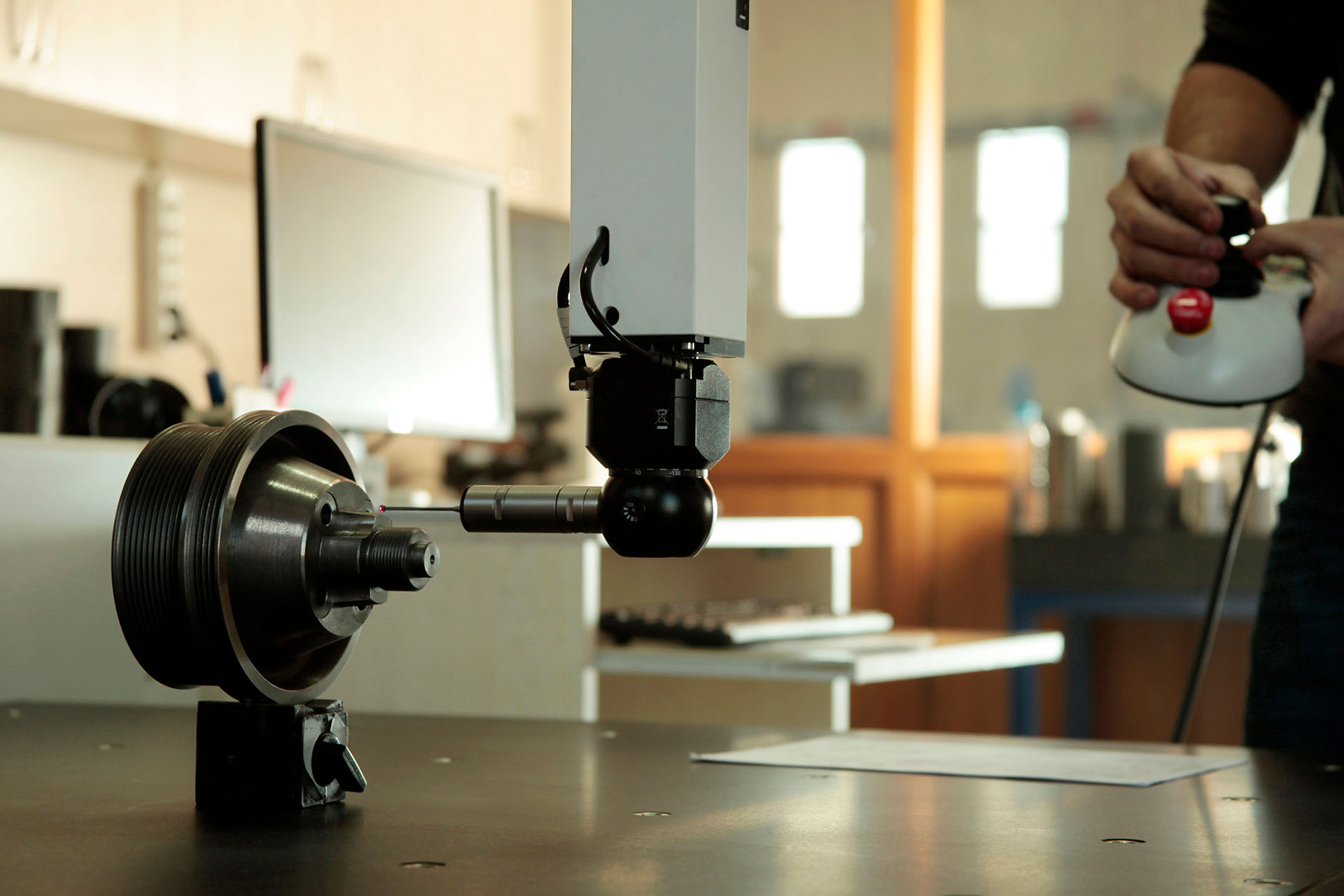
Metrology Services
Key Precision also offer metrology services, where accuracy meets efficiency to ensure the quality and precision of our customers injection-moulded components. With a dedicated team of skilled technicians and cutting-edge equipment, we offer a comprehensive range of metrology solutions tailored to meet your exact needs.
Our Metrology Engineers understand the critical importance of precise measurements for injection-moulded components. These components often require meticulous dimensional inspection to verify adherence to tight tolerances and regulatory standards, ensuring patient safety and product efficacy.
Our metrology services encompass techniques including coordinate measuring machines (CMM) and optical measurement. Whether you need to measure intricate geometries, verify critical dimensions, or assess surface finish and texture, we have the capabilities to deliver accurate and reliable results for your medical components.
With a commitment to excellence and a focus on regulatory compliance, we provide metrology services that meet the stringent requirements of each industry.
Whether you’re developing new products, conducting first-article inspections, or ensuring batch consistency, you can trust us to provide the precise measurements and analysis needed to maintain the highest standards of quality and safety.
Contact us today to learn more about our metrology services and how we can support your injection moulding needs.
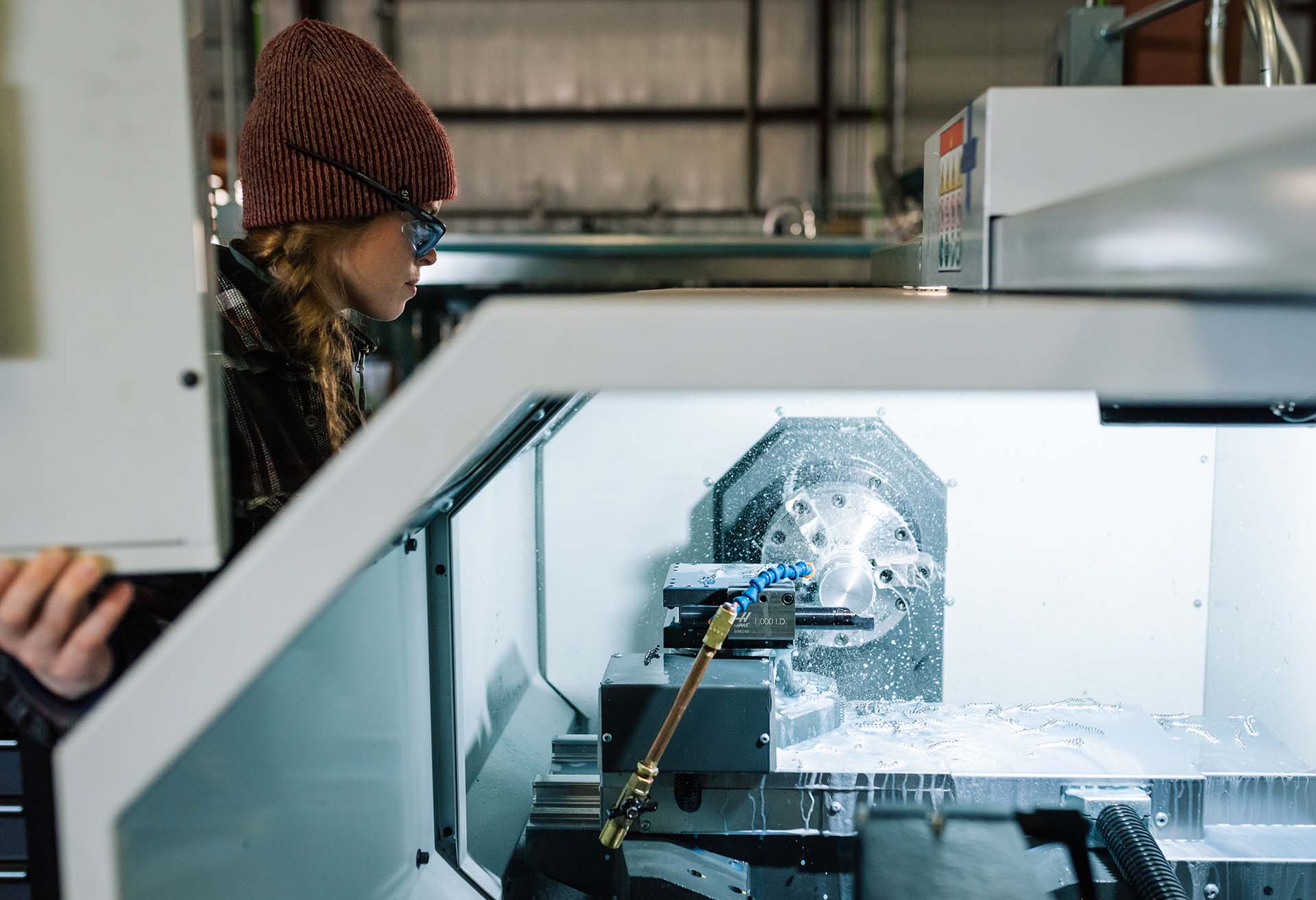
Precision Engineering
At Key Precision our medical device solution extends to offers a comprehensive range of precision engineering solutions tailored to meet your exact specifications and requirements.
At our cutting-edge facility, we leverage advanced technologies such as EDM (Electrical Discharge Machining) and wire erosion to achieve intricate shapes and fine details with unmatched precision and accuracy. Our multi-axis milling capabilities allow us to produce complex components with tight tolerances and superior surface finishes, while turning processes ensure optimal precision for cylindrical components.
In addition to machining capabilities, we offer advanced laser welding services for joining dissimilar materials and achieving precise welds in challenging applications. Our expertise extends to the design and manufacture of jigs and fixtures, essential tools for ensuring accuracy and repeatability in any manufacturing processes.
Whether you require prototyping, small-batch production, or high-volume manufacturing, our team of skilled engineers and technicians is committed to delivering excellence at every stage of the process.
Partner with us for your precision engineering needs and experience the difference that our commitment to quality, innovation, and precision can make. Contact us today to learn more about our capabilities and how we can help bring your vision to reality with precision-engineered solutions tailored to your unique requirements.

Mould Service & Repair
Declan and his team of highly skilled toolmakers are here to help. Offering a daily collection and delivery service our team are here to ensure a fast and efficient turnaround of your mould repairs and modification.
Certified to ISO 13485 and AS9100 Key Precision can offer you:
- Laser Welding
- EDM
- Wire Erosion
- CNC Machining
- DFM support
- Collection & Delivery Service
- Mould Trialling Service
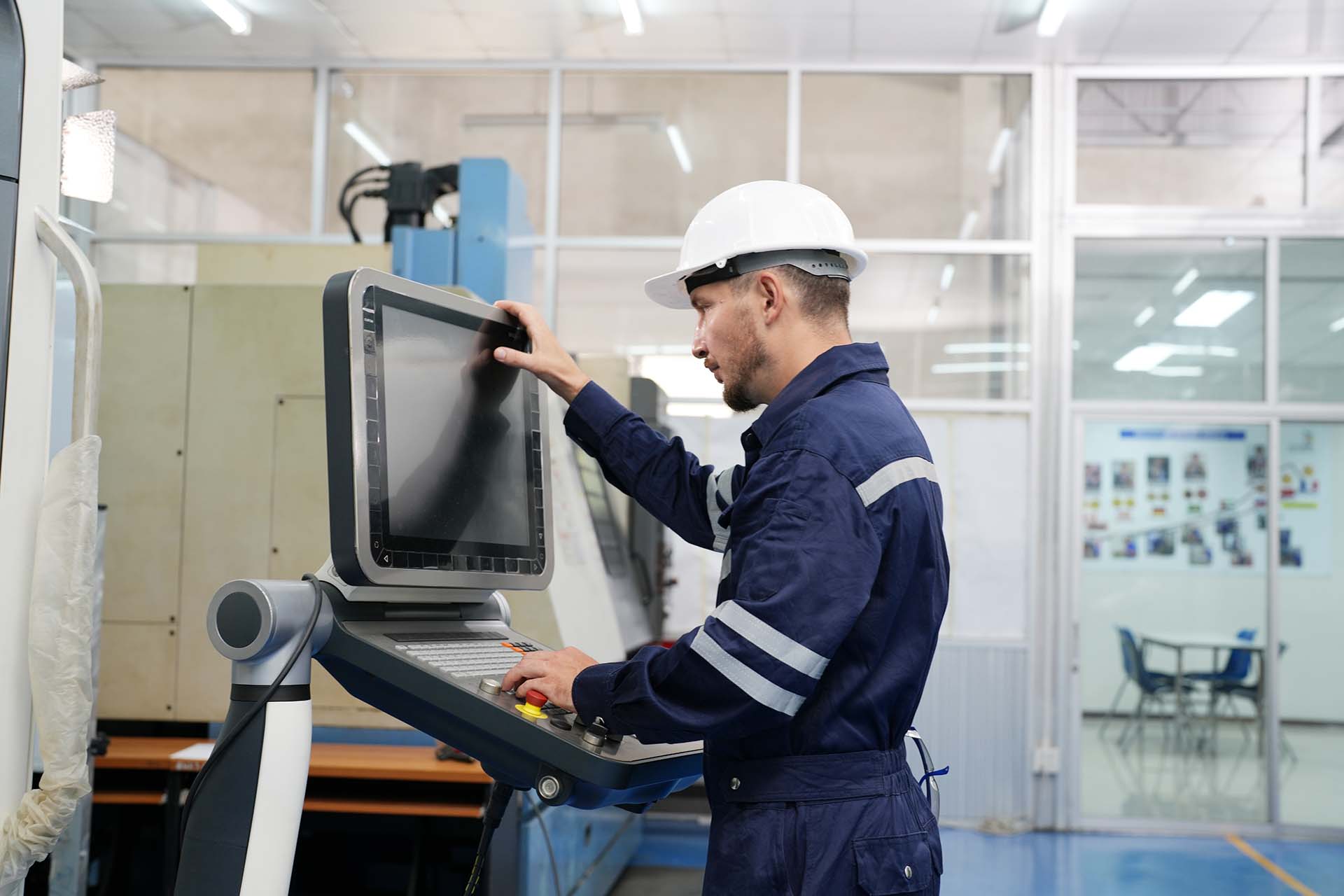
Product Design & Design for Manufacturing (DFM)
In the realm of contract injection moulding, product design and Design for Manufacture (DFM) are pivotal stages that dictate the efficiency, quality, and cost-effectiveness of the entire manufacturing process. As contract manufacturers, our expertise lies in seamlessly translating our clients’ conceptual designs into manufacturable products that meet their precise specifications and requirements.
Product design serves as the foundation of the manufacturing journey, where intricate details and functional requirements are crafted into a tangible blueprint. Through collaborative engagement with our clients, we use our expertise in injection moulding to optimise designs for manufacturability, ensuring that each component is tailored to withstand the rigors of the production process while maximising efficiency and minimising material waste.
Design for Manufacture (DFM) combines creative ideas with practical manufacturing needs. It’s about designing products in a way that considers how they will be made. At Key our team of seasoned engineers meticulously evaluates each design iteration, identifying opportunities for streamlining production processes, minimising tooling costs, and enhancing part performance. Utilising advanced CAD/CAM software and simulation tools, we validate designs in virtual environments, exploring and addressing potential manufacturing challenges and optimising part geometry for injection moulding.
The critical relationship between product design and Design for Manufacture (DFM) is fundamental to our commitment to delivering exceptional value and innovation to our clients. Through proactive collaboration, design refinement, and rigorous validation, we empower our clients to bring their concepts to life with precision, efficiency, and cost-effectiveness.
As trusted partners in contract injection moulding, we stand ready to collaborate with you at every stage of the product development journey, from initial design conception to final production, ensuring that your vision is realised with unparalleled quality and reliability.
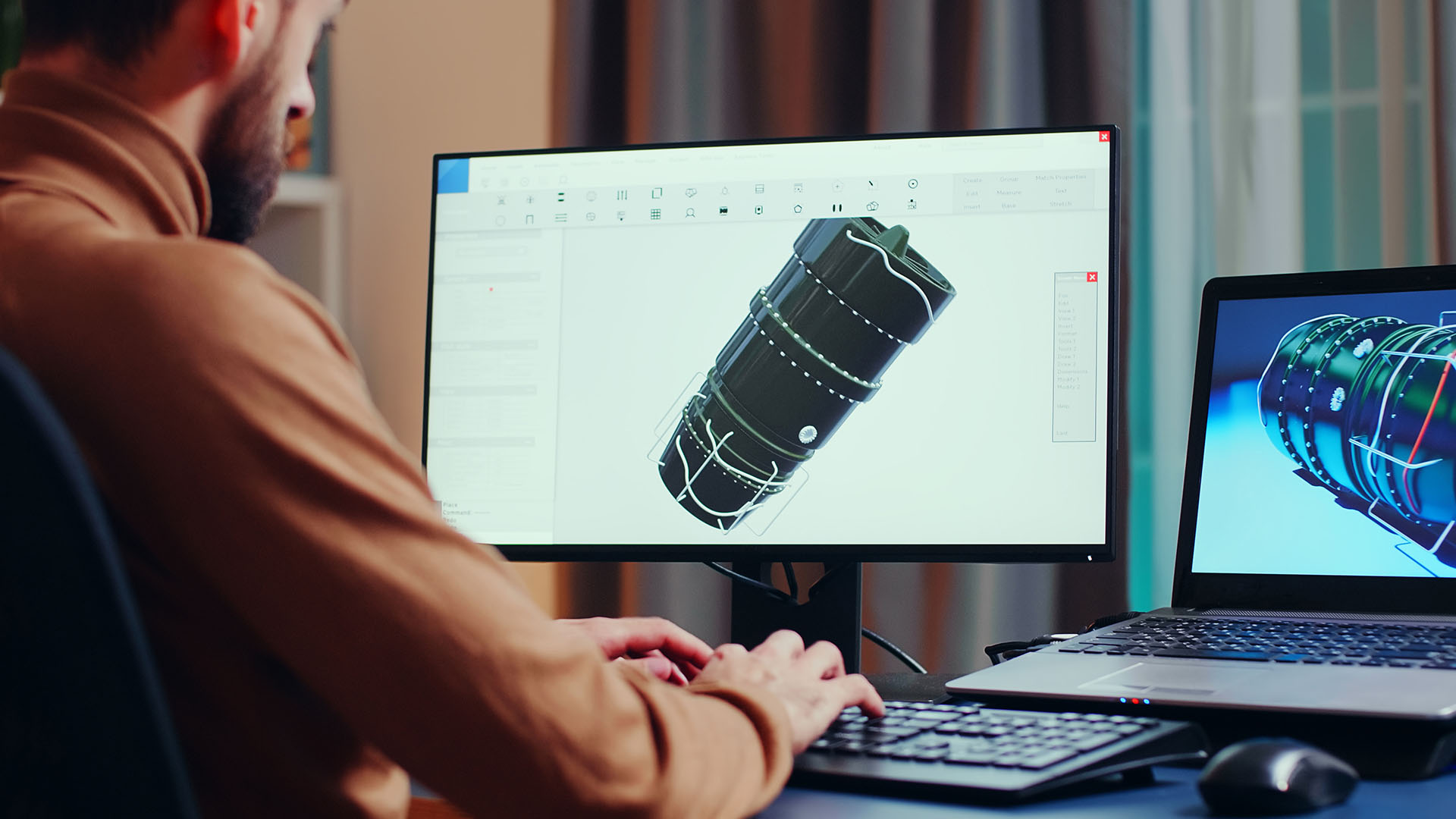
Mould Design & Manufacture
At Key Precision we can offer our customers a premium mould manufacturing services, where precision meets innovation to bring your designs to life. With decades of experience and a team of master mould makers, we specialize in delivering high-quality moulds tailored to your exact specifications.
At our state-of-the-art facility, we leverage advanced precision machining techniques such as EDM, wire erosion, milling, and turning to create moulds with unparalleled accuracy and consistency. Our in-house capabilities, combined with strategic partnerships with external approved partners, ensure that we have the flexibility and expertise to handle projects of any complexity or scale.
From prototyping to production, our dedicated engineers work closely with you every step of the way to ensure that your moulds are manufactured to the highest standards of quality and precision.
Partner with us for your mould manufacturing needs and experience the difference that our commitment to excellence and many years of industry experience can make.
Contact us today to learn more about our capabilities and how we can help bring your vision to reality with precision-crafted moulds that exceed your expectations.
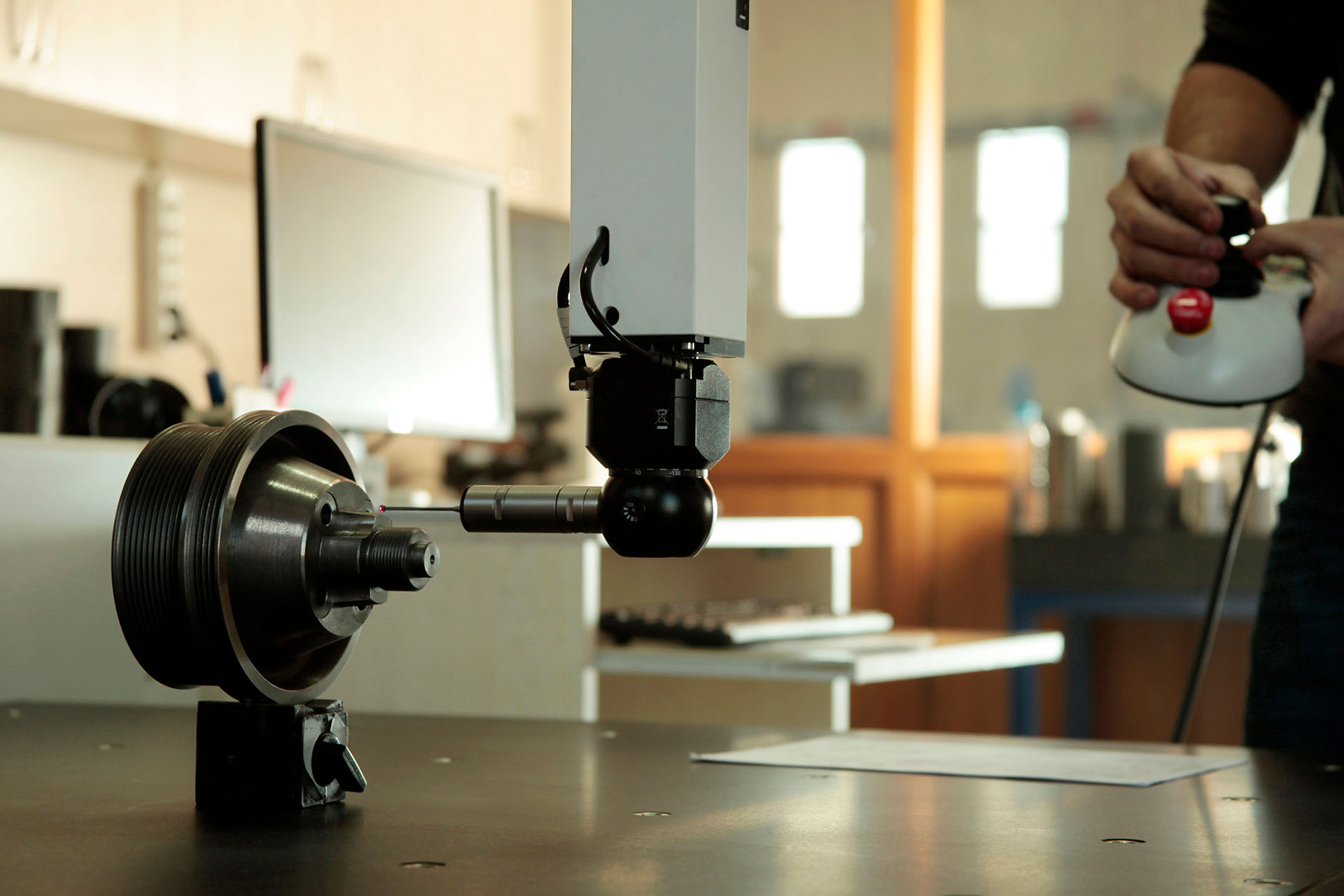
Metrology Services
Key Precision also offer metrology services, where accuracy meets efficiency to ensure the quality and precision of our customers injection-moulded components. With a dedicated team of skilled technicians and cutting-edge equipment, we offer a comprehensive range of metrology solutions tailored to meet your exact needs.
Our Metrology Engineers understand the critical importance of precise measurements for injection-moulded components. These components often require meticulous dimensional inspection to verify adherence to tight tolerances and regulatory standards, ensuring patient safety and product efficacy.
Our metrology services encompass techniques including coordinate measuring machines (CMM) and optical measurement. Whether you need to measure intricate geometries, verify critical dimensions, or assess surface finish and texture, we have the capabilities to deliver accurate and reliable results for your medical components.
With a commitment to excellence and a focus on regulatory compliance, we provide metrology services that meet the stringent requirements of each industry.
Whether you’re developing new products, conducting first-article inspections, or ensuring batch consistency, you can trust us to provide the precise measurements and analysis needed to maintain the highest standards of quality and safety.
Contact us today to learn more about our metrology services and how we can support your injection moulding needs.
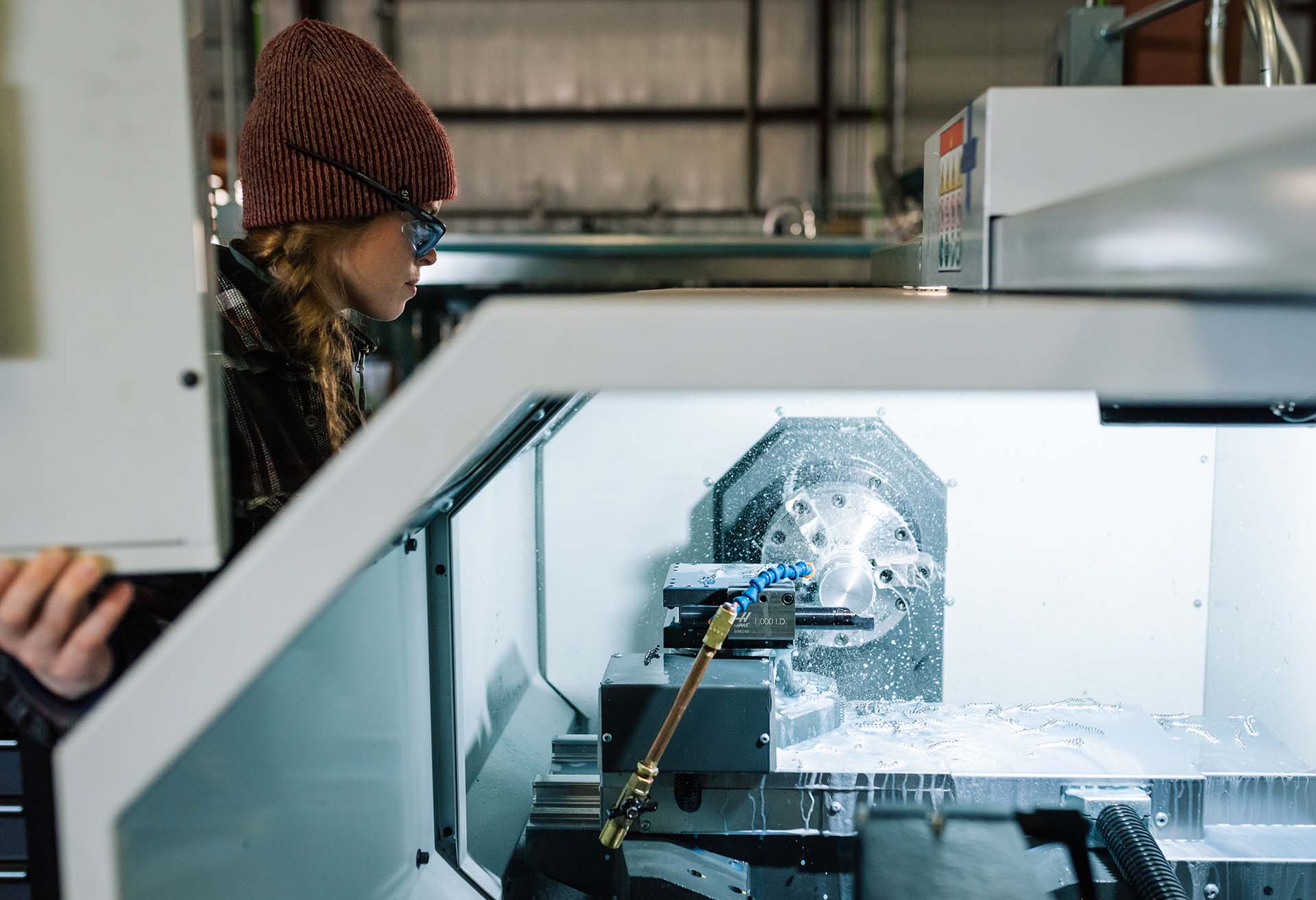
Precision Engineering
At Key Precision our medical device solution extends to offers a comprehensive range of precision engineering solutions tailored to meet your exact specifications and requirements.
At our cutting-edge facility, we leverage advanced technologies such as EDM (Electrical Discharge Machining) and wire erosion to achieve intricate shapes and fine details with unmatched precision and accuracy. Our multi-axis milling capabilities allow us to produce complex components with tight tolerances and superior surface finishes, while turning processes ensure optimal precision for cylindrical components.
In addition to machining capabilities, we offer advanced laser welding services for joining dissimilar materials and achieving precise welds in challenging applications. Our expertise extends to the design and manufacture of jigs and fixtures, essential tools for ensuring accuracy and repeatability in any manufacturing processes.
Whether you require prototyping, small-batch production, or high-volume manufacturing, our team of skilled engineers and technicians is committed to delivering excellence at every stage of the process.
Partner with us for your precision engineering needs and experience the difference that our commitment to quality, innovation, and precision can make. Contact us today to learn more about our capabilities and how we can help bring your vision to reality with precision-engineered solutions tailored to your unique requirements.
About Key
Key Plastics Ltd was founded in 1986 and remains a family-operated business.
We aim to excel in the field of injection moulding by combining precision, innovation, and integrity. We operate through three specialised divisions, each dedicated to delivering excellence.
Key Plastics, our Contract Plastics Moulding division.
Key Medical, our Medical device Moulding division and cleanroom facility.
Key Precision, our Design & Engineering division.
These three divisions, united, drive Key Plastics Ltd forward in our pursuit of excellence, innovation, and social responsibility. Guided by our values, we aim to catalyse positive change, pushing the limits of what’s achievable in the plastics industry while remaining steadfast in our commitment to precision, quality, and customer satisfaction.
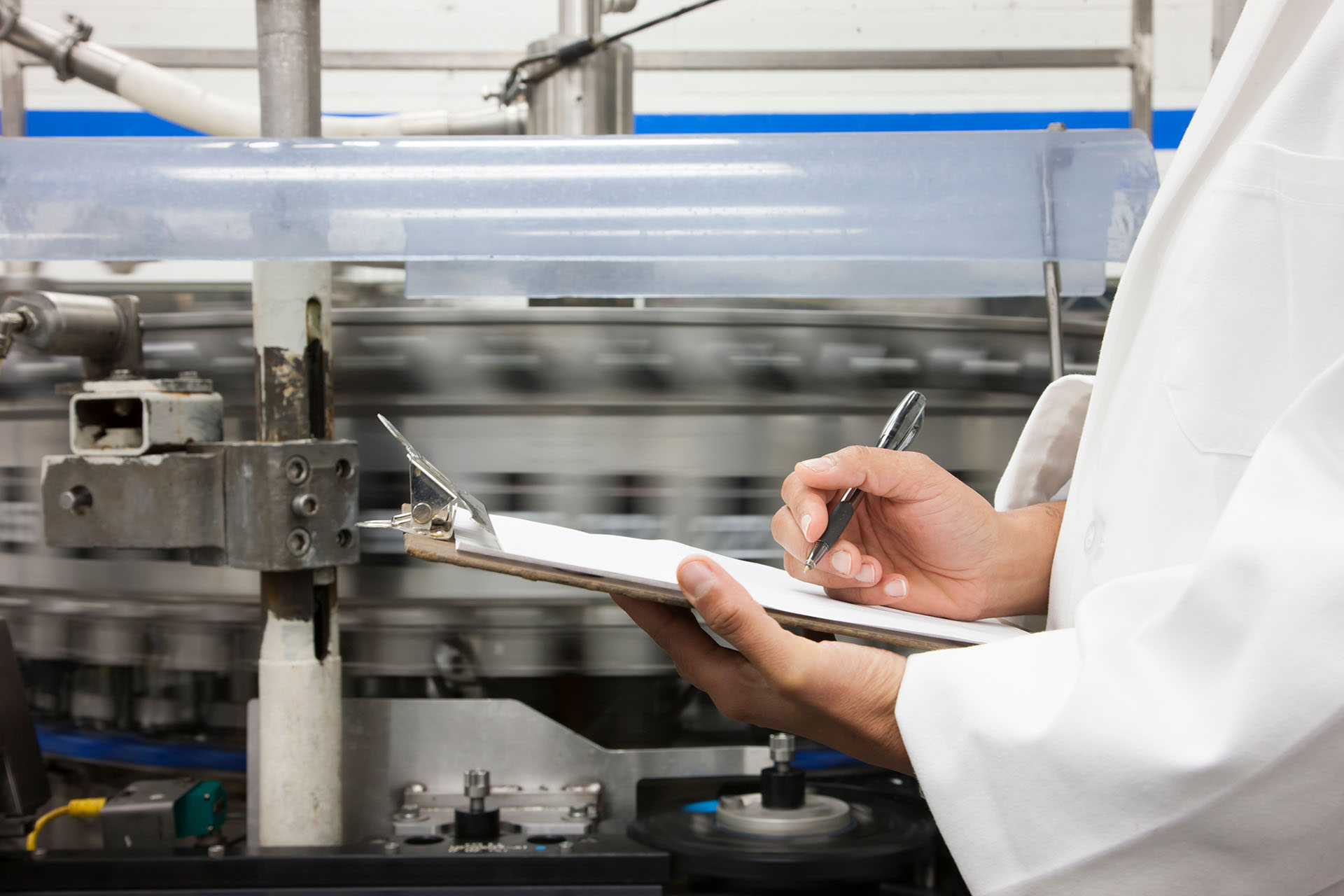
Key Values
Quality Excellence
We are committed to delivering products of the highest quality, adhering to rigorous standards at every stage of production.
Innovation
We foster a culture of innovation, constantly seeking new and improved methods to enhance efficiency, productivity, and product offerings.
Integrity
We conduct our business with honesty, transparency, and ethical integrity, maintaining the trust of our customers, employees, and stakeholders.
Customer Focus
Our customers are at the center of everything we do. We strive to understand their needs, exceed their expectations, and build lasting partnerships based on mutual respect and satisfaction.
Continuous Improvement
We embrace a mindset of continuous improvement, constantly evaluating and refining our processes, systems, and products to remain competitive and stay ahead of industry trends.
Safety
The safety and well-being of our employees, customers, and communities are paramount. We are committed to maintaining a safe work environment and adhering to the highest standards of occupational health and safety.
Safety
The safety and well-being of our employees, customers, and communities are paramount. We are committed to maintaining a safe work environment and adhering to the highest standards of occupational health and safety.
Environmental Responsibility
We are dedicated to minimizing our environmental footprint through sustainable practices, resource conservation, and the development of eco-friendly products and processes.
Teamwork & Collaboration
We value collaboration, diversity, and teamwork, recognising that our collective talents and perspectives drive innovation and success.
Community Engagement
We actively engage with and support the communities in which we operate, contributing positively to social, economic, and environmental initiatives.
Accountability
Heading
Lorem ipsum dolor sit amet, consectetur adipiscing elit. Maecenas pretium dapibus ante vel vehicula.