At Key Plastics, our mission is to lead with precision, innovation, and integrity in the world of injection moulding. Comprising three distinct divisions, each with a specialised focus, we are dedicated to delivering excellence in every aspect of our operations.
At Key Medical we are committed to contributing to advancements in medical technology, ensuring the production of high-quality, safe, and reliable components that make a positive impact on global healthcare outcomes.
ABOUT KEY Plastics Ltd
At Key Plastics, our mission is to lead with precision, innovation, and integrity in the world of injection moulding. Comprising three distinct divisions, each with a specialised focus, we are dedicated to delivering excellence in every aspect of our operations.
We offer comprehensive project support from concept and prototyping through validation to mass production under one roof.
Our clients not only benefit from a streamlined procurement process but the assurance of receiving a cost-effective solution. With guaranteed on-time deliveries, we uphold superior quality levels ensuring that your project is executed seamlessly and efficiently.
Establishing long lasting relationships with our customer base ensures a reliable and trustworthy service.
Every project is treated with equal diligence, ensuring the highest attainable quality and excellence.
Flexibility is essential in the design and manufacturing of products, and our team takes pride in demonstrating agility in every project
Establishing long lasting relationships with our customer base ensures a reliable and trustworthy service.
Every project is treated with equal diligence, ensuring the highest attainable quality and excellence.
Flexibility is essential in the design and manufacturing of products, and our team takes pride in demonstrating agility in every project
Medical
To help stakeholders in government and business make smart decisions.
- Video Production
- Writing
- Community management
- Performance
Aerospace
To help stakeholders in government and business make smart decisions.
- Video Production
- Writing
- Community management
- Performance
Telecoms
To help stakeholders in government and business make smart decisions.
- Video Production
- Writing
- Community management
- Performance
Engineering
To help stakeholders in government and business make smart decisions.
- Video Production
- Writing
- Community management
- Performance
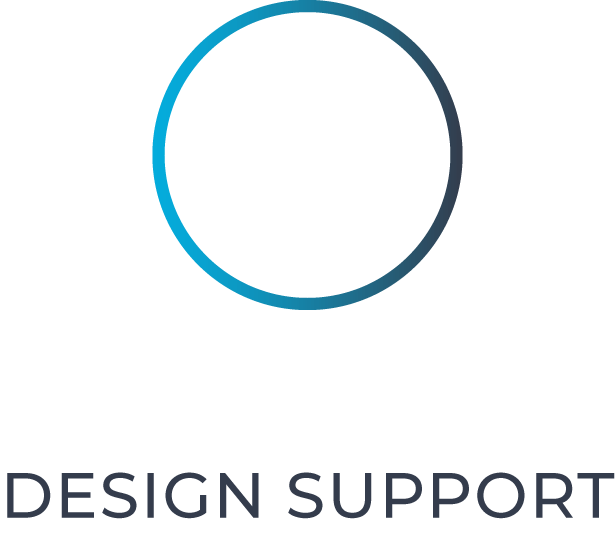
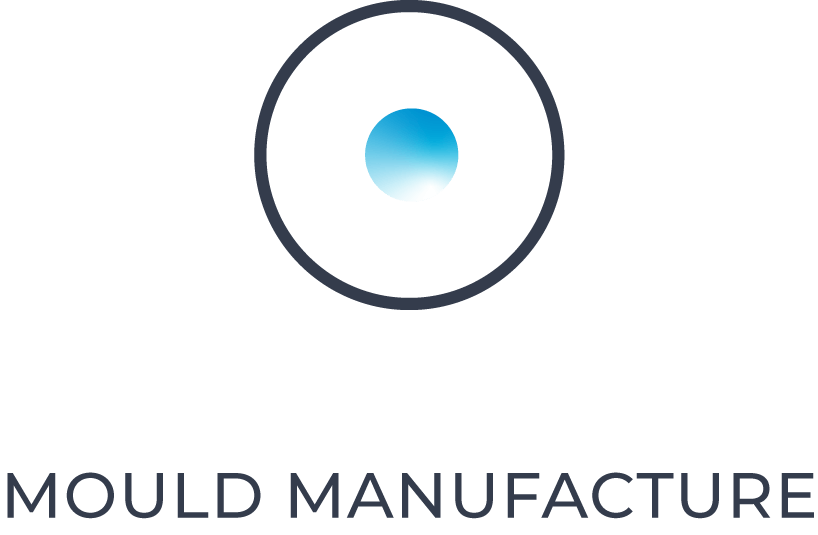
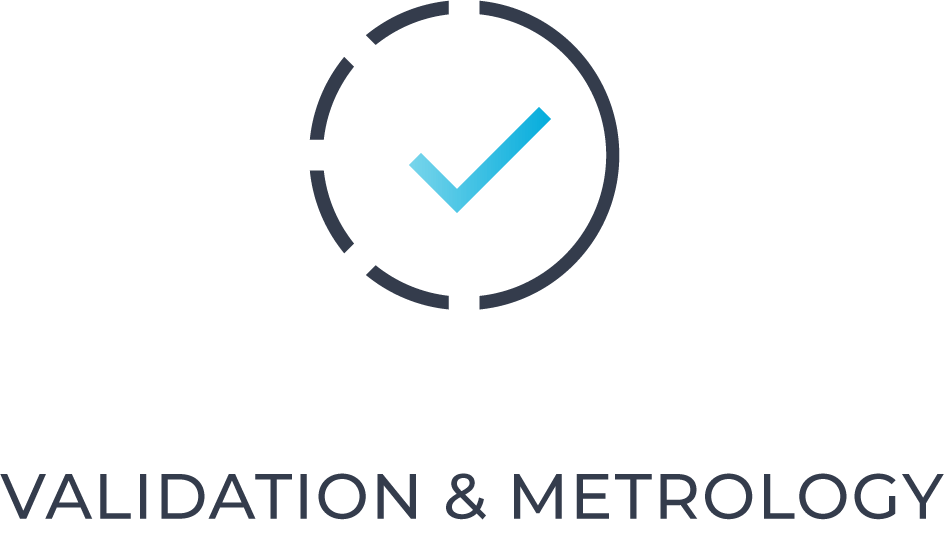
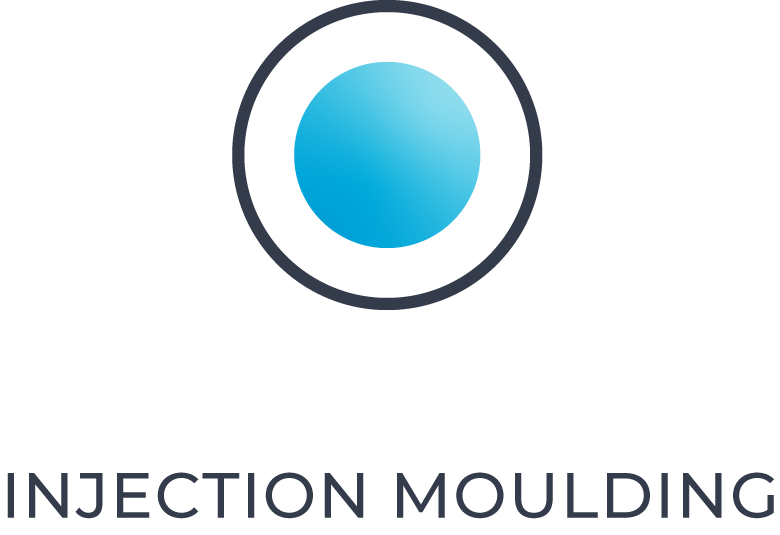
- Injection Moulding
- Validation & Acceptance Testing
-
Product Design & Design for
Manufacturing (DFM) - Mould Manufacture
- Metrology Services
- Precision Engineering
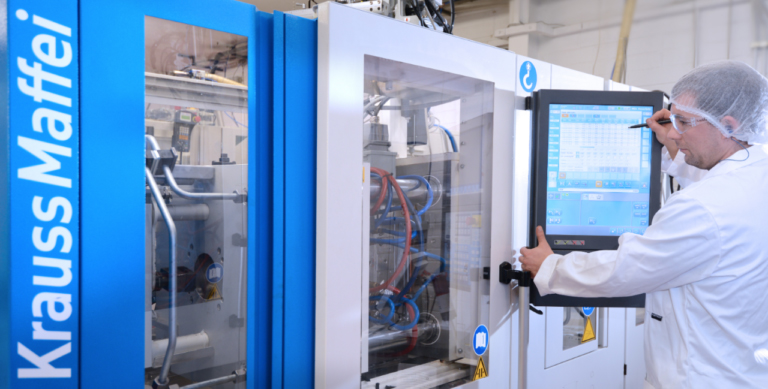
Injection Moulding
We specialise in delivering exceptional quality and consistency in every injection-moulded part. Our advanced machinery and stringent protocols allow us to produce components with tight tolerances and intricate geometries, meeting the exact specifications of our clients across various industries.
Whether you need prototypes, low-volume production runs, or high-volume manufacturing, Key Plastics is equipped to handle projects of any scale with efficiency and precision.
From concept to mass production, our experienced team works closely with you to understand your needs, provide expert guidance, and deliver customised solutions that exceed expectations.
Partner with us for your moulding needs and experience the unmatched capabilities of our facility in bringing your ideas to life with unparalleled precision and reliability.
Contact us today to learn more about our capabilities and how we can help you achieve your goals with confidence and precision.
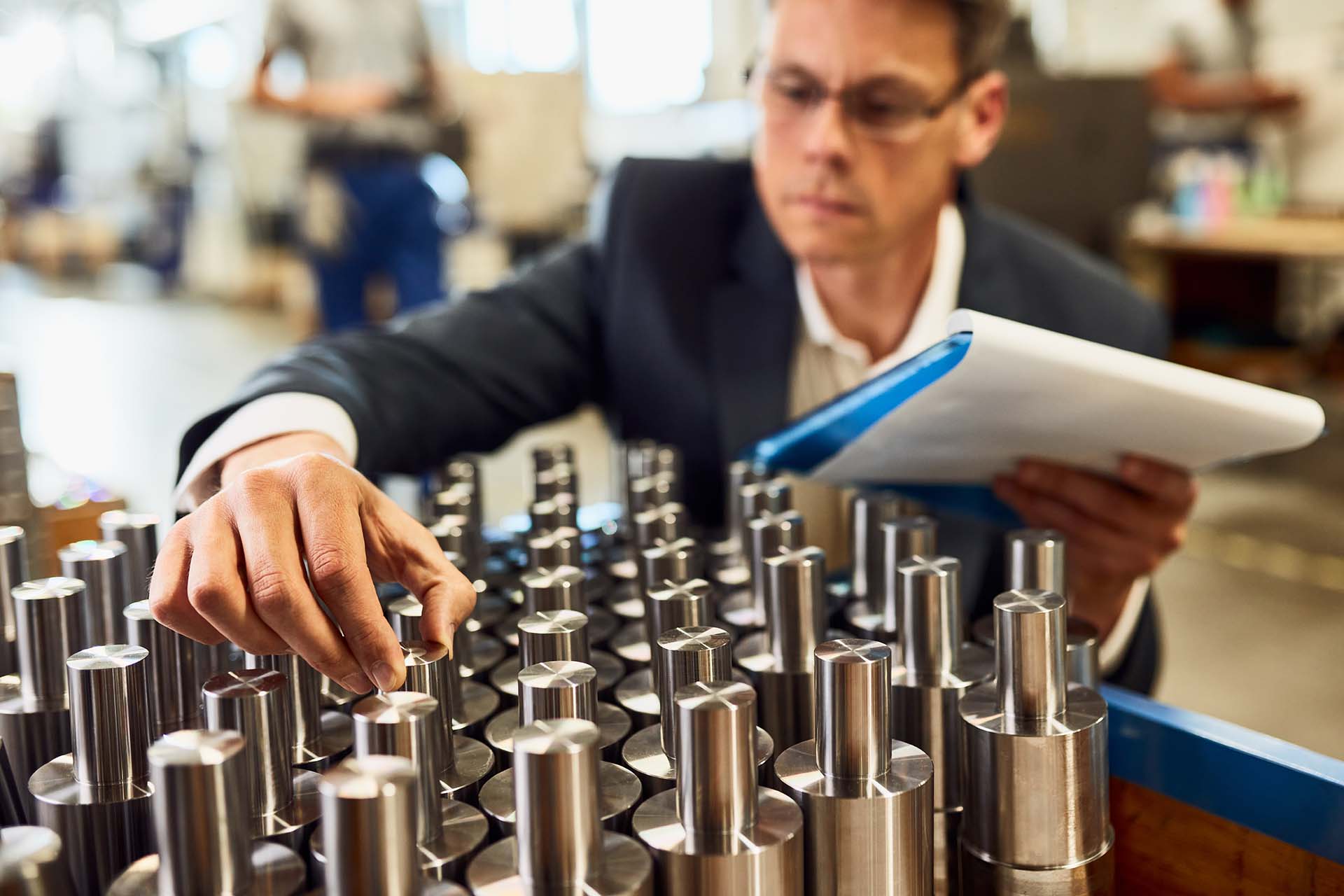
Validation & Acceptance Testing
In plastics moulding & manufacturing, validation and acceptance testing are pivotal stages that underpin the integrity and success of the entire production process. As contract manufacturers, we understand the critical importance of ensuring that every plastic moulded part meets the rigorous standards and specifications outlined by our customers.
Through production validation, we strive to optimise and refine the manufacturing process to deliver consistent, repeatable results. Through meticulous monitoring and control of key parameters such as temperature, pressure, and cycle time, we validate that our production facilities are fully capable of meeting the precise tolerances and quality requirements specified by our customers.
Our Process Validation Steps include:
- Establishment of Objectives
- Design of Experiments
- Installation Qualification (IQ)
- Operations Qualification (OQ)
- Performance Qualification (PQ)
- Process Monitoring & Control
- Document & Review
- Revalidation
As injection mould manufacturers, our unwavering commitment to validation and acceptance testing serves as the cornerstone of our partnership with clients, underpinning mutual trust, confidence, and satisfaction.
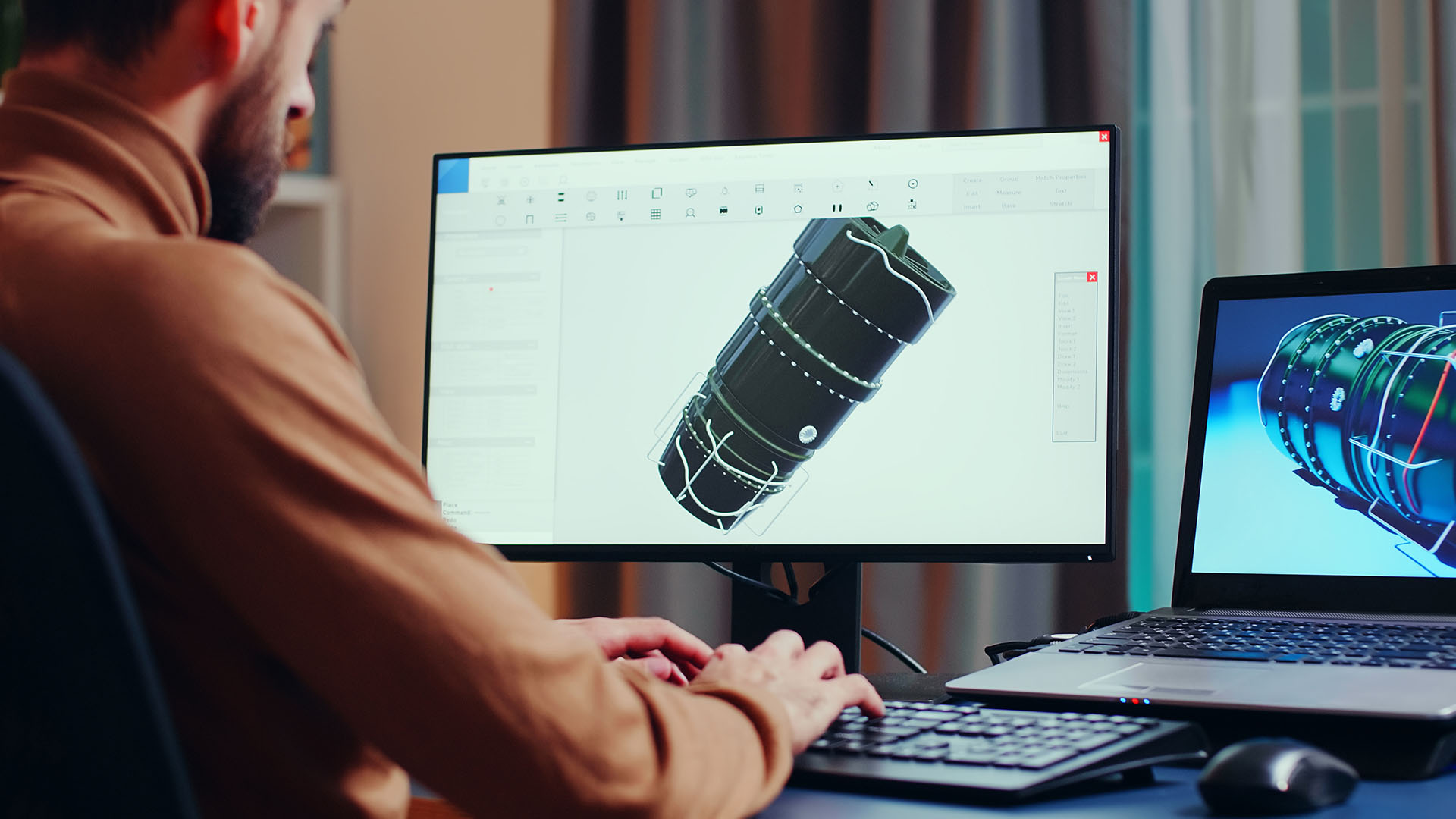
Product Design & Design for Manufacturing (DFM)
Product design and Design for Manufacture (DFM) are pivotal stages that dictate the efficiency, quality, and cost-effectiveness of the entire manufacturing process. As contract manufacturers, our expertise lies in seamlessly translating our clients’ conceptual designs into manufacturable products that meet their precise specifications and requirements.
Product Design serves as the foundation of the manufacturing journey, where intricate details and functional requirements are crafted into a tangible blueprint. Through collaborative engagement with our clients, we use our expertise in injection moulding to optimise designs for manufacturability, ensuring that each component is tailored to withstand the rigors of the production process while maximising efficiency and minimising material waste.
Design for Manufacture (DFM) combines creative ideas with practical manufacturing needs. It’s about designing products in a way that considers how they will be made. At Key, our team of seasoned engineers meticulously evaluates each design iteration, identifying opportunities for streamlining production processes, minimising tooling costs, and enhancing part performance. Utilising advanced CAD/CAM software and simulation tools, we validate designs in virtual environments, exploring and addressing potential manufacturing challenges and optimising part geometry for injection moulding.
The critical relationship between product design and DFM is fundamental to our commitment to delivering exceptional value and innovation to our clients. Through proactive collaboration, design refinement, and rigorous validation, we empower our clients to bring their concepts to life with precision, efficiency, and cost-effectiveness.
We stand ready to collaborate with you at every stage of the product development journey, from initial design conception to final production, ensuring that your vision is realised with unparalleled quality and reliability.
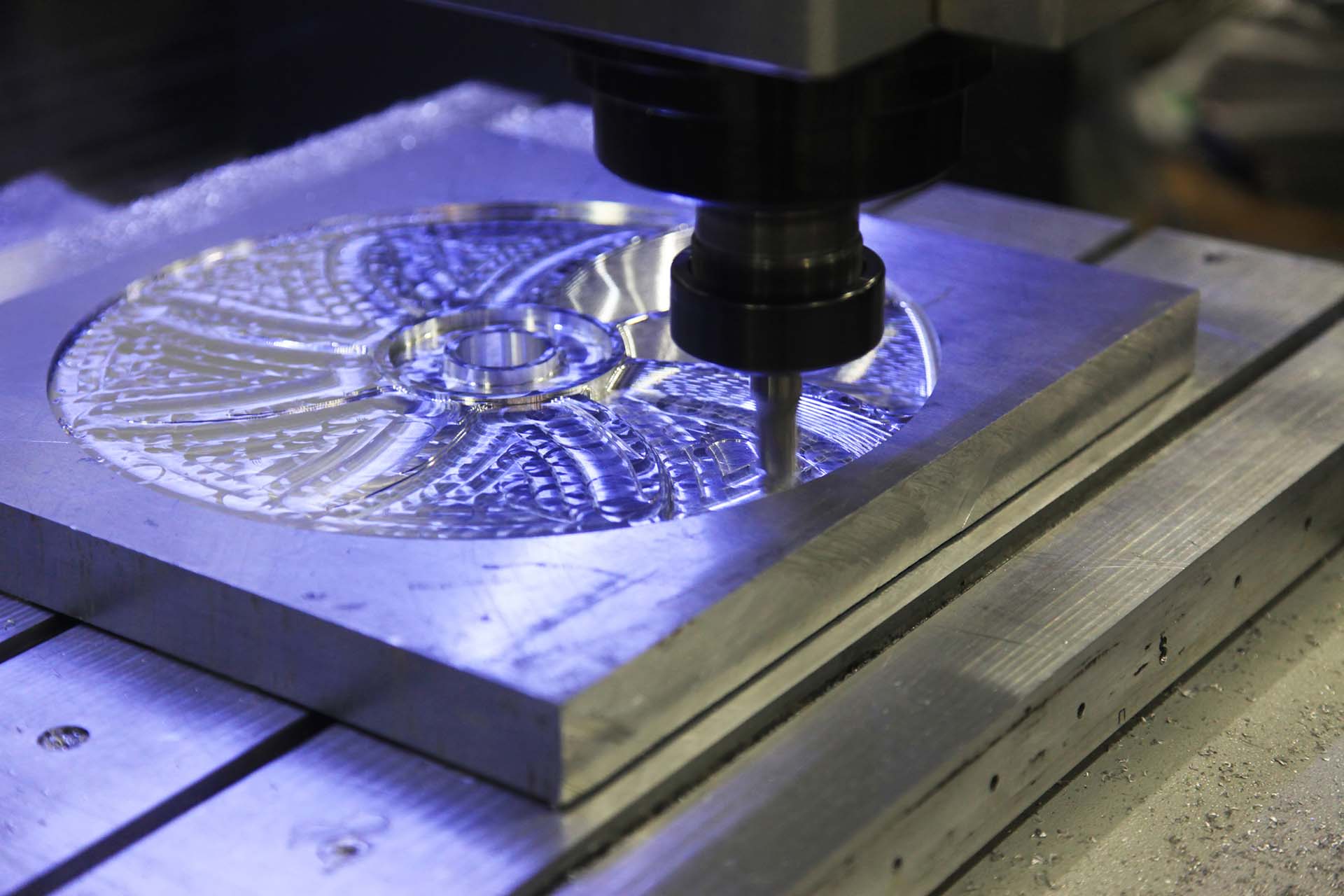
Mould Manufacture
Utilising our vast experience in precision engineering, Key Precision we can offer our customers a premium mould manufacturing services, where precision meets innovation to bring your designs to life. With decades of experience and a team of master mould makers, we specialise in delivering high-quality moulds tailored to your exact specifications.
At our state-of-the-art facility, we leverage advanced precision machining techniques such as EDM, wire erosion, milling, and turning to create moulds with unparalleled accuracy and consistency. Our in-house capabilities, combined with strategic partnerships with external approved partners, ensure that we have the flexibility and expertise to handle projects of any complexity or scale.
From prototyping to production, our dedicated engineers work closely with you every step of the way to ensure that your moulds are manufactured to the highest standards of quality and precision.
Partner with us for your injection mould manufacturing needs and experience the difference that our commitment to excellence and many years of industry experience can make.
Contact us today to learn more about our capabilities and how we can help bring your vision to reality with precision-crafted moulds that exceed your expectations.
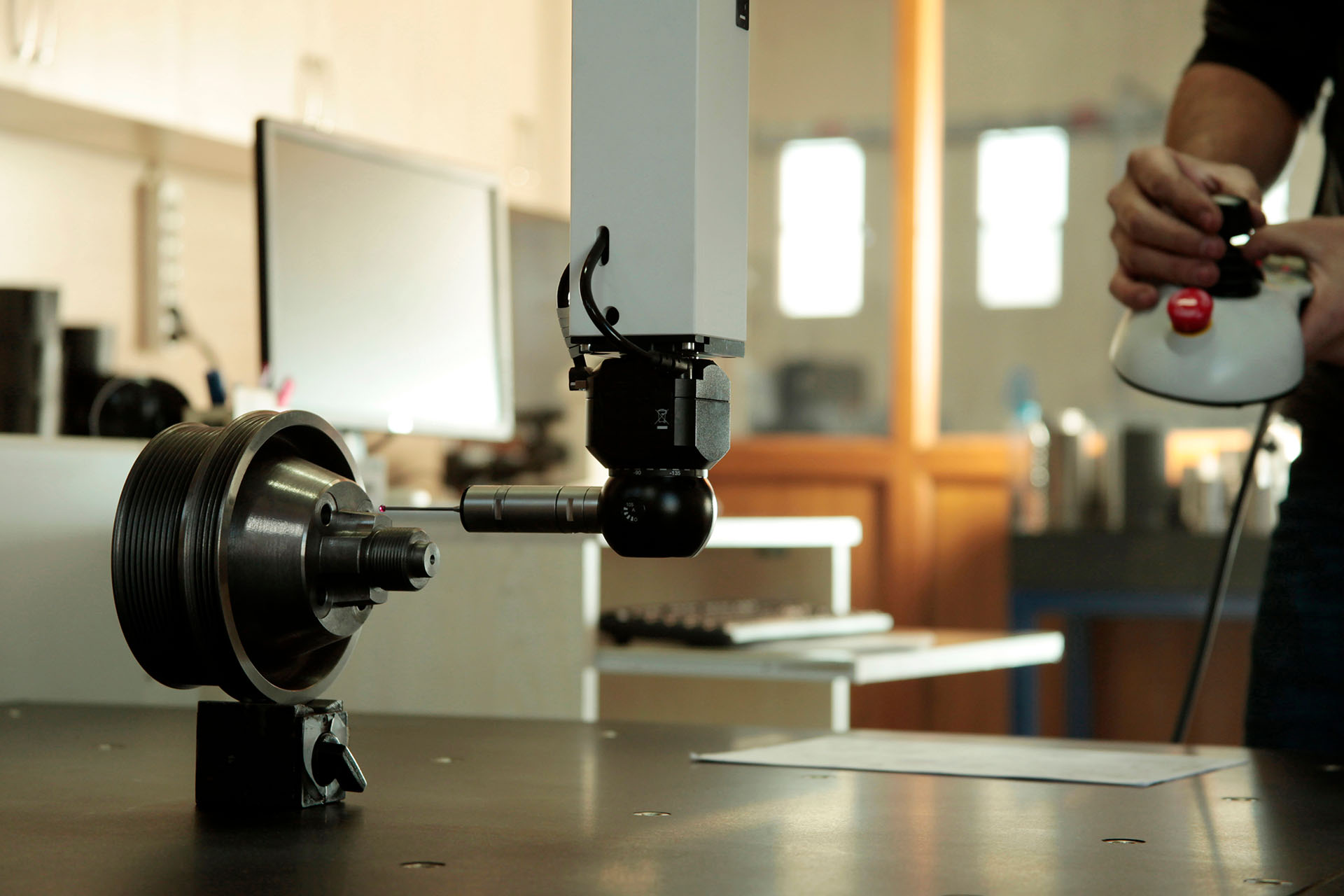
Metrology Services
Key also offer metrology services, where accuracy meets efficiency to ensure the quality and precision of our customers injection-moulded components. With a dedicated team of skilled technicians and cutting-edge equipment, we offer a comprehensive range of metrology solutions tailored to meet your exact needs, no matter the industry.
Our Metrology Engineers understand the critical importance of precise measurements for injection-moulded components. These components often require meticulous dimensional inspection to verify adherence to tight tolerances and regulatory standards, ensuring patient safety and product efficacy.
Our metrology services encompass techniques including coordinate measuring machines (CMM) and optical measurement. Whether you need to measure intricate geometries, verify critical dimensions, or assess surface finish and texture, we have the capabilities to deliver accurate and reliable results for your components.
Whether you’re developing new products, conducting first-article inspections, or ensuring batch consistency, you can trust us to provide the precise measurements and analysis needed to maintain the highest standards of quality and safety.
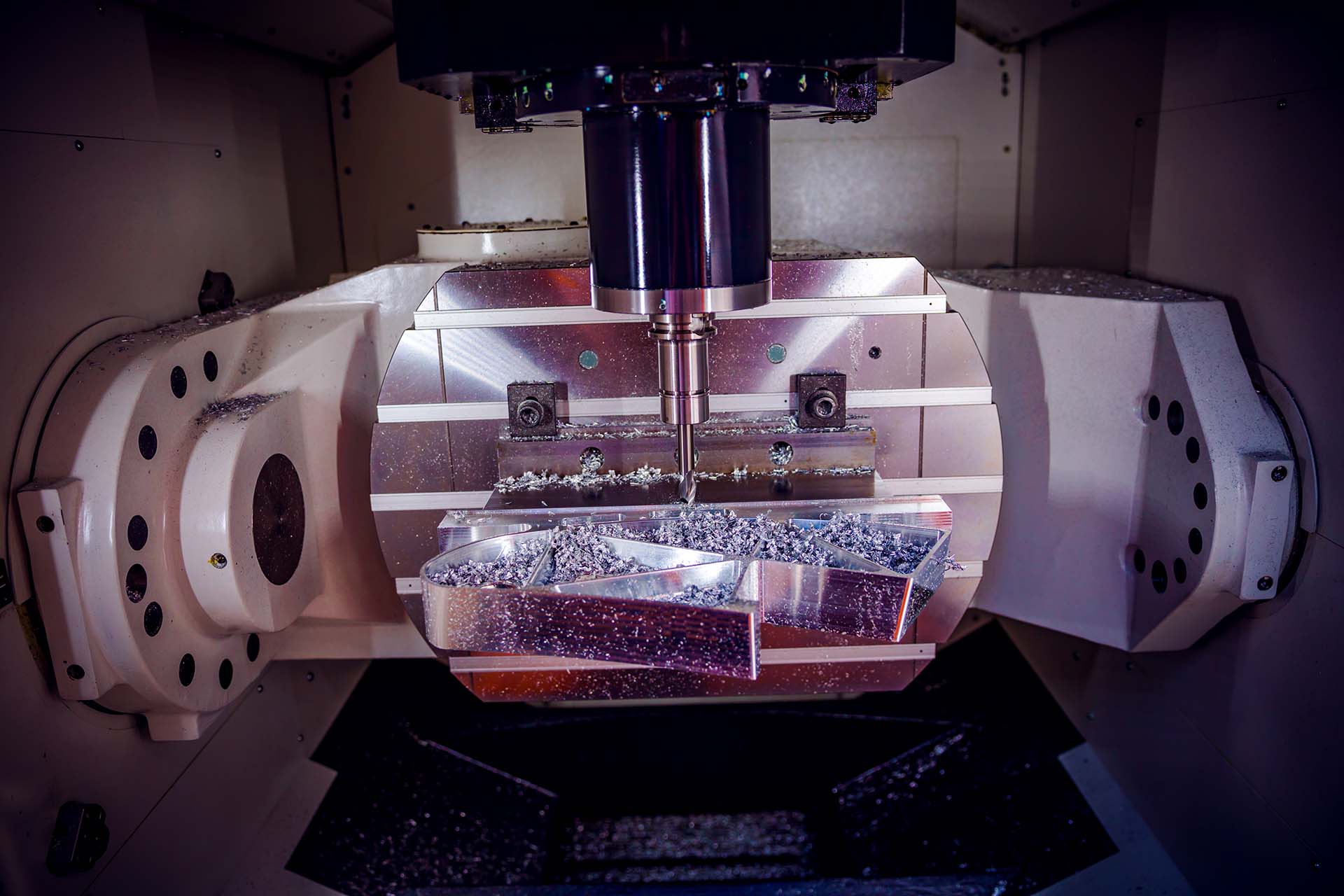
Precision Engineering
At our cutting-edge facility, we leverage advanced technologies such as EDM (Electrical Discharge Machining) and wire erosion to achieve intricate shapes and fine details with unmatched precision and accuracy. Our multi-axis milling capabilities allow us to produce complex components with tight tolerances and superior surface finishes, while turning processes ensure optimal precision for cylindrical components.
In addition to machining capabilities, we offer advanced laser welding services for joining dissimilar materials and achieving precise welds in challenging applications. Our expertise extends to the design and manufacture of jigs and fixtures, essential tools for ensuring accuracy and repeatability in any manufacturing processes.
Whether you require prototyping, small-batch production, or high-volume manufacturing, our team of skilled engineers and technicians is committed to delivering excellence at every stage of the process.
Partner with us for your precision engineering needs and experience the difference that our commitment to quality, innovation, and precision can make. Contact our Key Precision division to learn more about our capabilities and how we can help bring your vision to reality with precision-engineered solutions tailored to your unique requirements.
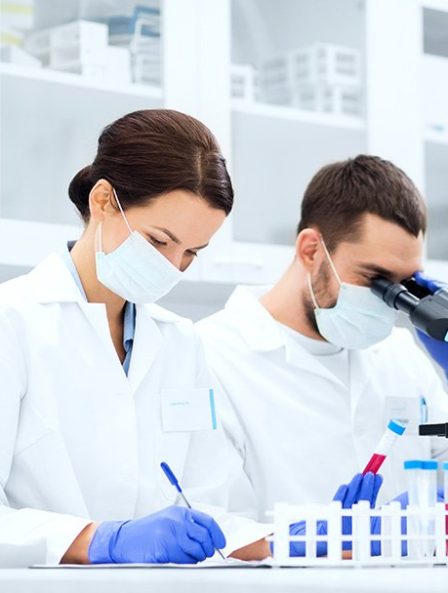
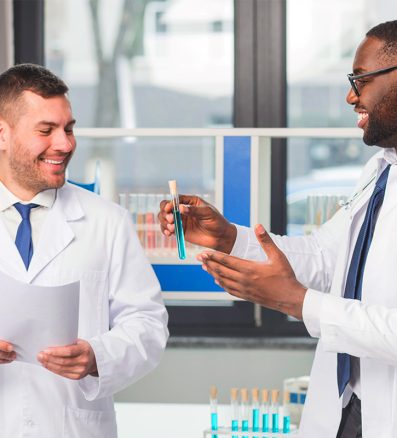
Injection Moulding
12 x Krauss Maffei 50T to 80T
5 x Krauss Maffei 110T to 350T
2 x Negri Bossi 830T & 850T
1 x Fanuc 80T
Certified Class 7 Cleanroom
Sepro Robotics /Full beam & Pick and Place
Processing 20+ Polymer types
Quality Lab with CMM measurement
Dedicated Assembly Room
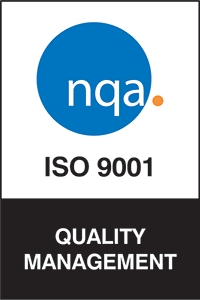
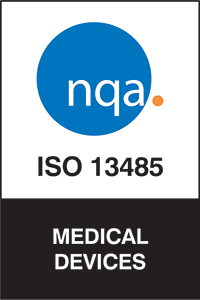
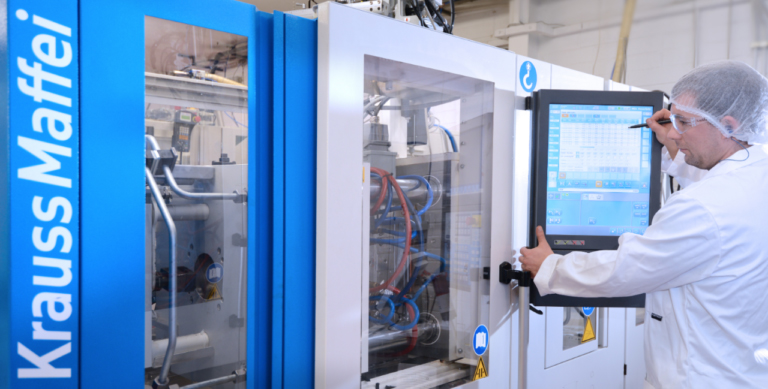
Injection Moulding
We specialise in delivering exceptional quality and consistency in every injection-moulded part. Our advanced machinery and stringent protocols allow us to produce components with tight tolerances and intricate geometries, meeting the exact specifications of our clients across various industries.
Whether you need prototypes, low-volume production runs, or high-volume manufacturing, Key Plastics is equipped to handle projects of any scale with efficiency and precision.
From concept to mass production, our experienced team works closely with you to understand your needs, provide expert guidance, and deliver customised solutions that exceed expectations.
Partner with us for your moulding needs and experience the unmatched capabilities of our facility in bringing your ideas to life with unparalleled precision and reliability.
Contact us today to learn more about our capabilities and how we can help you achieve your goals with confidence and precision.
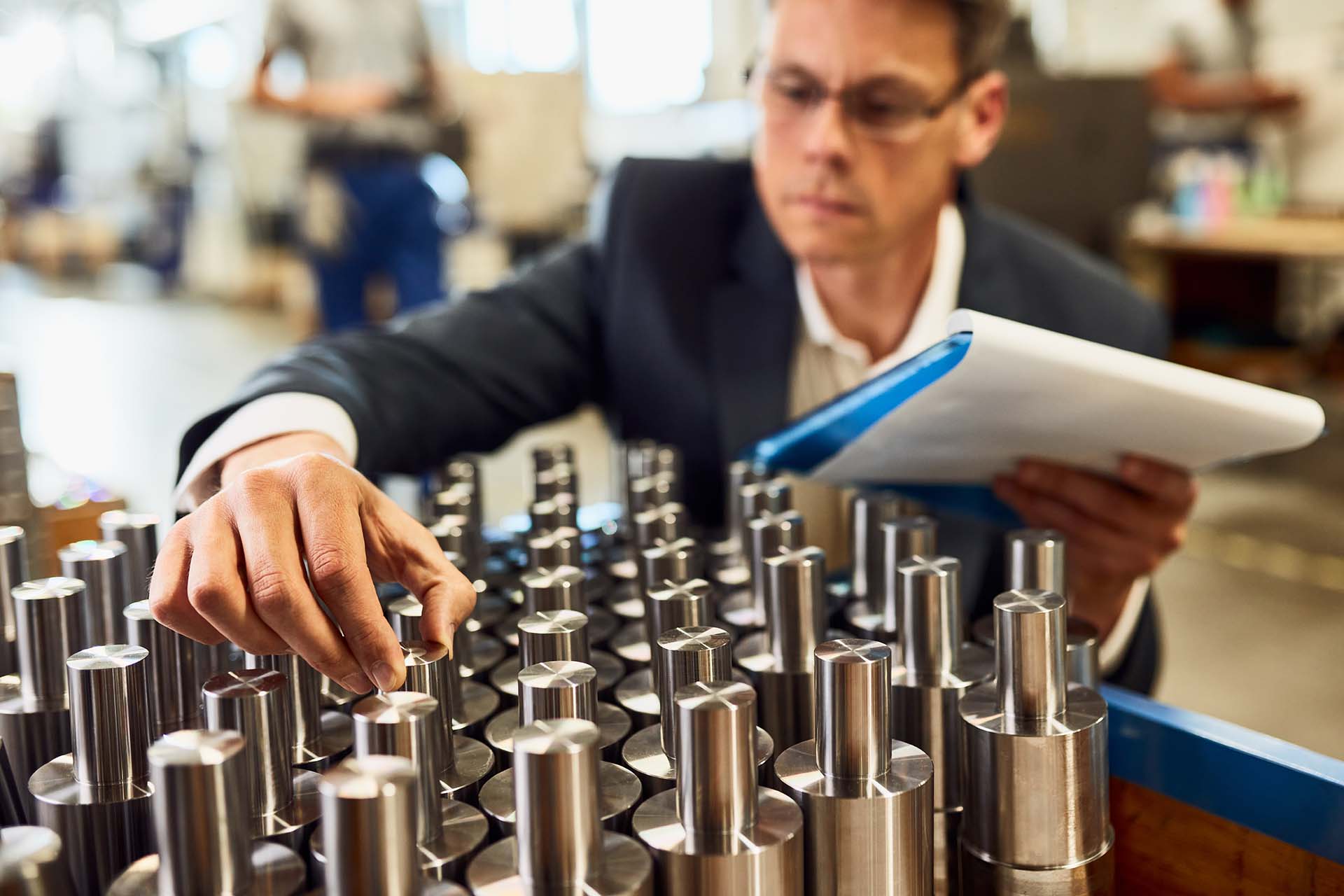
Validation & Acceptance Testing
In plastics moulding & manufacturing, validation and acceptance testing are pivotal stages that underpin the integrity and success of the entire production process. As contract manufacturers, we understand the critical importance of ensuring that every plastic moulded part meets the rigorous standards and specifications outlined by our customers.
Through production validation, we strive to optimise and refine the manufacturing process to deliver consistent, repeatable results. Through meticulous monitoring and control of key parameters such as temperature, pressure, and cycle time, we validate that our production facilities are fully capable of meeting the precise tolerances and quality requirements specified by our customers.
Our Process Validation Steps include:
- Establishment of Objectives
- Design of Experiments
- Installation Qualification (IQ)
- Operations Qualification (OQ)
- Performance Qualification (PQ)
- Process Monitoring & Control
- Document & Review
- Revalidation
As injection mould manufacturers, our unwavering commitment to validation and acceptance testing serves as the cornerstone of our partnership with clients, underpinning mutual trust, confidence, and satisfaction.
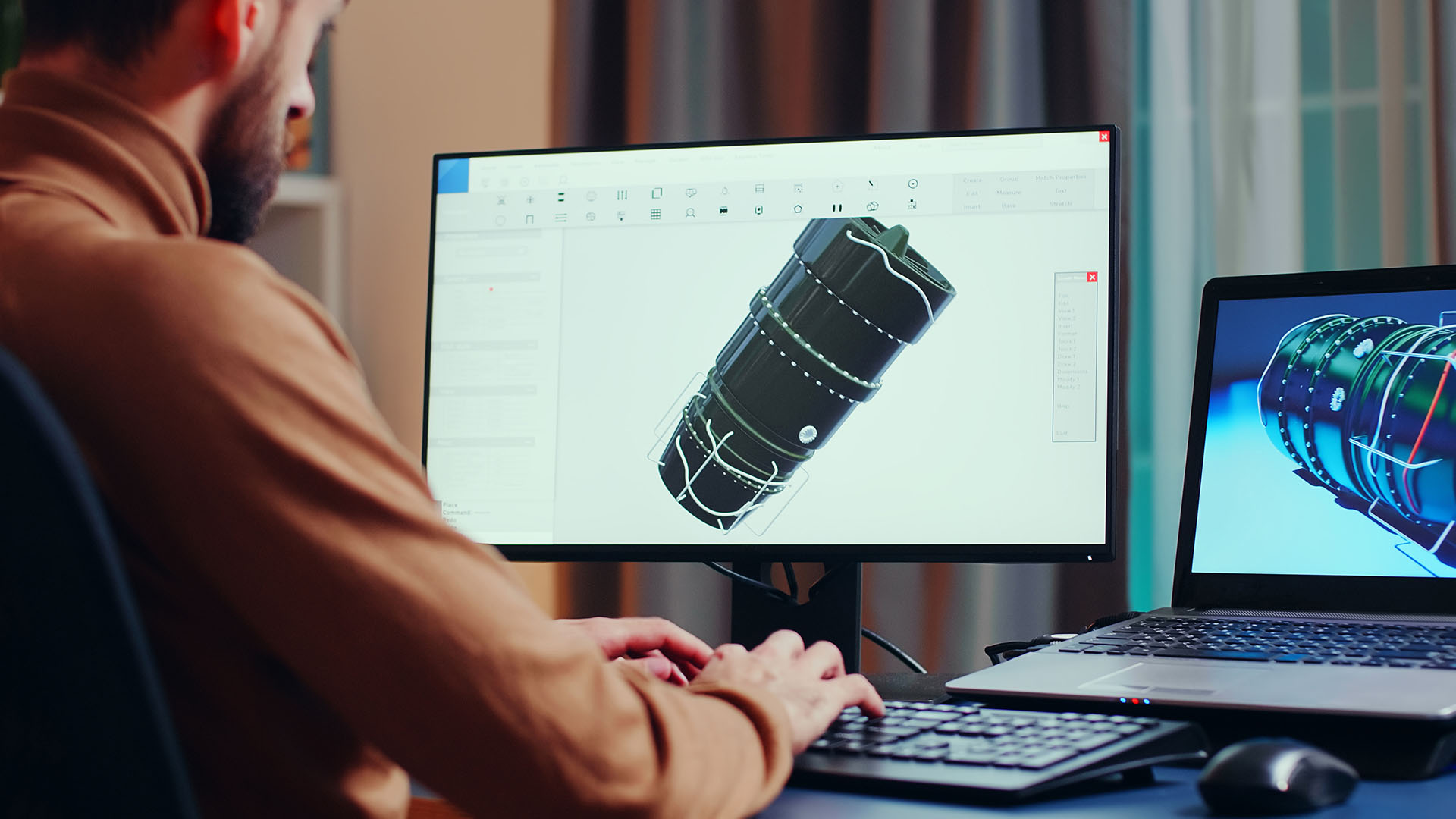
Product Design & Design for Manufacturing (DFM)
Product design and Design for Manufacture (DFM) are pivotal stages that dictate the efficiency, quality, and cost-effectiveness of the entire manufacturing process. As contract manufacturers, our expertise lies in seamlessly translating our clients’ conceptual designs into manufacturable products that meet their precise specifications and requirements.
Product Design serves as the foundation of the manufacturing journey, where intricate details and functional requirements are crafted into a tangible blueprint. Through collaborative engagement with our clients, we use our expertise in injection moulding to optimise designs for manufacturability, ensuring that each component is tailored to withstand the rigors of the production process while maximising efficiency and minimising material waste.
Design for Manufacture (DFM) combines creative ideas with practical manufacturing needs. It’s about designing products in a way that considers how they will be made. At Key, our team of seasoned engineers meticulously evaluates each design iteration, identifying opportunities for streamlining production processes, minimising tooling costs, and enhancing part performance. Utilising advanced CAD/CAM software and simulation tools, we validate designs in virtual environments, exploring and addressing potential manufacturing challenges and optimising part geometry for injection moulding.
The critical relationship between product design and DFM is fundamental to our commitment to delivering exceptional value and innovation to our clients. Through proactive collaboration, design refinement, and rigorous validation, we empower our clients to bring their concepts to life with precision, efficiency, and cost-effectiveness.
We stand ready to collaborate with you at every stage of the product development journey, from initial design conception to final production, ensuring that your vision is realised with unparalleled quality and reliability.
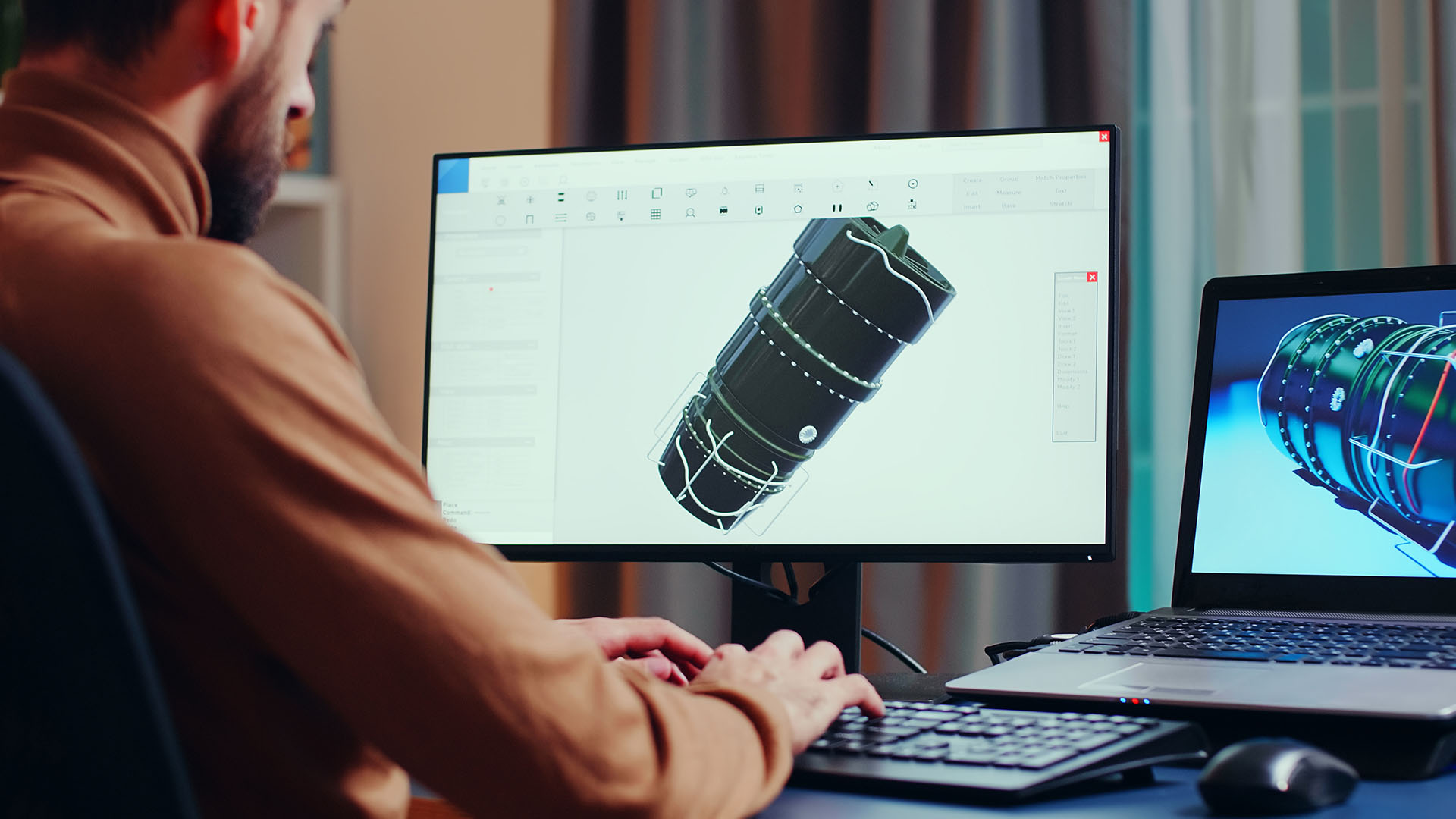
Product Design & Design for Manufacturing (DFM)
Product design and Design for Manufacture (DFM) are pivotal stages that dictate the efficiency, quality, and cost-effectiveness of the entire manufacturing process. As contract manufacturers, our expertise lies in seamlessly translating our clients’ conceptual designs into manufacturable products that meet their precise specifications and requirements.
Product Design serves as the foundation of the manufacturing journey, where intricate details and functional requirements are crafted into a tangible blueprint. Through collaborative engagement with our clients, we use our expertise in injection moulding to optimise designs for manufacturability, ensuring that each component is tailored to withstand the rigors of the production process while maximising efficiency and minimising material waste.
Design for Manufacture (DFM) combines creative ideas with practical manufacturing needs. It’s about designing products in a way that considers how they will be made. At Key, our team of seasoned engineers meticulously evaluates each design iteration, identifying opportunities for streamlining production processes, minimising tooling costs, and enhancing part performance. Utilising advanced CAD/CAM software and simulation tools, we validate designs in virtual environments, exploring and addressing potential manufacturing challenges and optimising part geometry for injection moulding.
The critical relationship between product design and DFM is fundamental to our commitment to delivering exceptional value and innovation to our clients. Through proactive collaboration, design refinement, and rigorous validation, we empower our clients to bring their concepts to life with precision, efficiency, and cost-effectiveness.
We stand ready to collaborate with you at every stage of the product development journey, from initial design conception to final production, ensuring that your vision is realised with unparalleled quality and reliability.
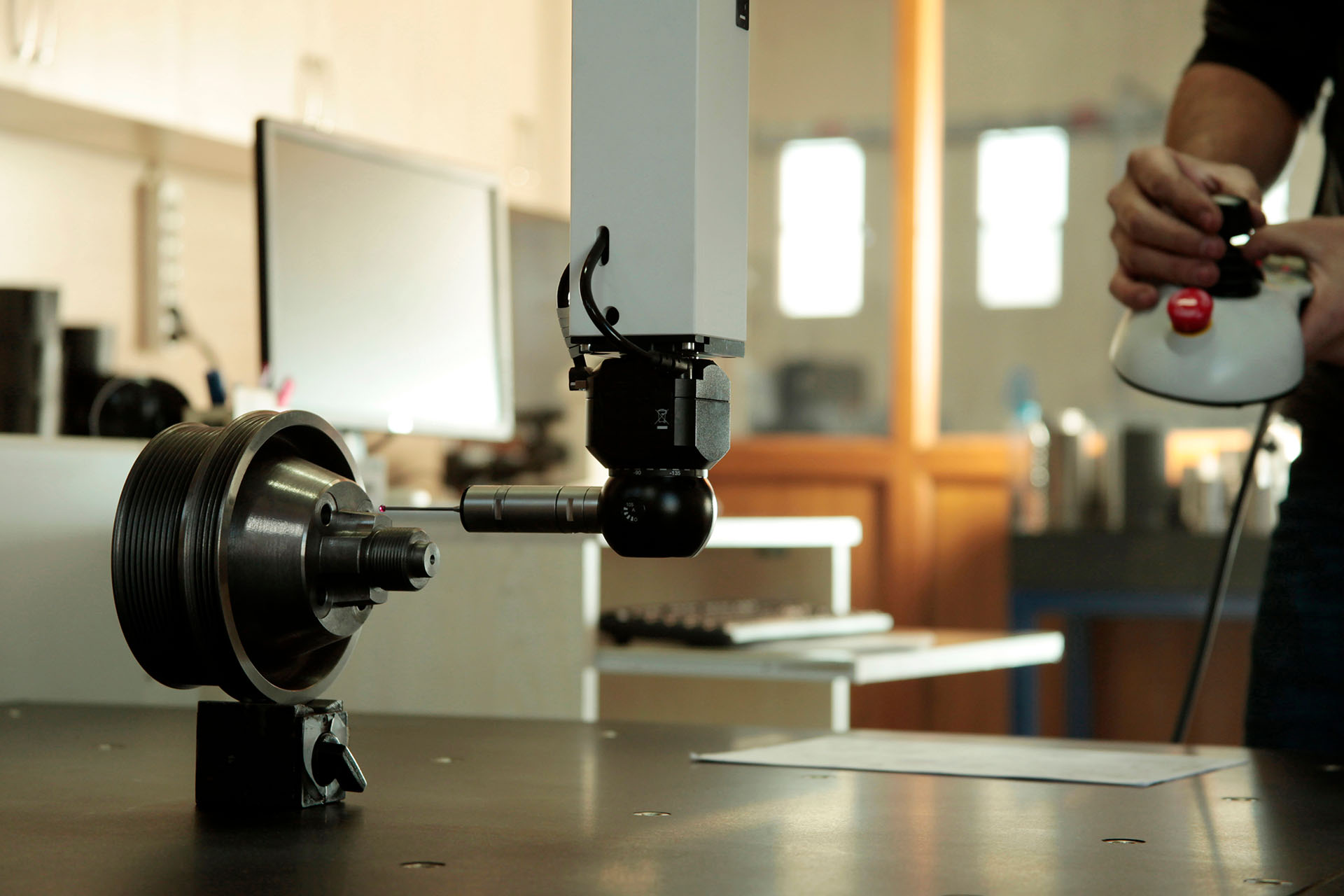
Metrology Services
Key also offer metrology services, where accuracy meets efficiency to ensure the quality and precision of our customers injection-moulded components. With a dedicated team of skilled technicians and cutting-edge equipment, we offer a comprehensive range of metrology solutions tailored to meet your exact needs, no matter the industry.
Our Metrology Engineers understand the critical importance of precise measurements for injection-moulded components. These components often require meticulous dimensional inspection to verify adherence to tight tolerances and regulatory standards, ensuring patient safety and product efficacy.
Our metrology services encompass techniques including coordinate measuring machines (CMM) and optical measurement. Whether you need to measure intricate geometries, verify critical dimensions, or assess surface finish and texture, we have the capabilities to deliver accurate and reliable results for your components.
Whether you’re developing new products, conducting first-article inspections, or ensuring batch consistency, you can trust us to provide the precise measurements and analysis needed to maintain the highest standards of quality and safety.
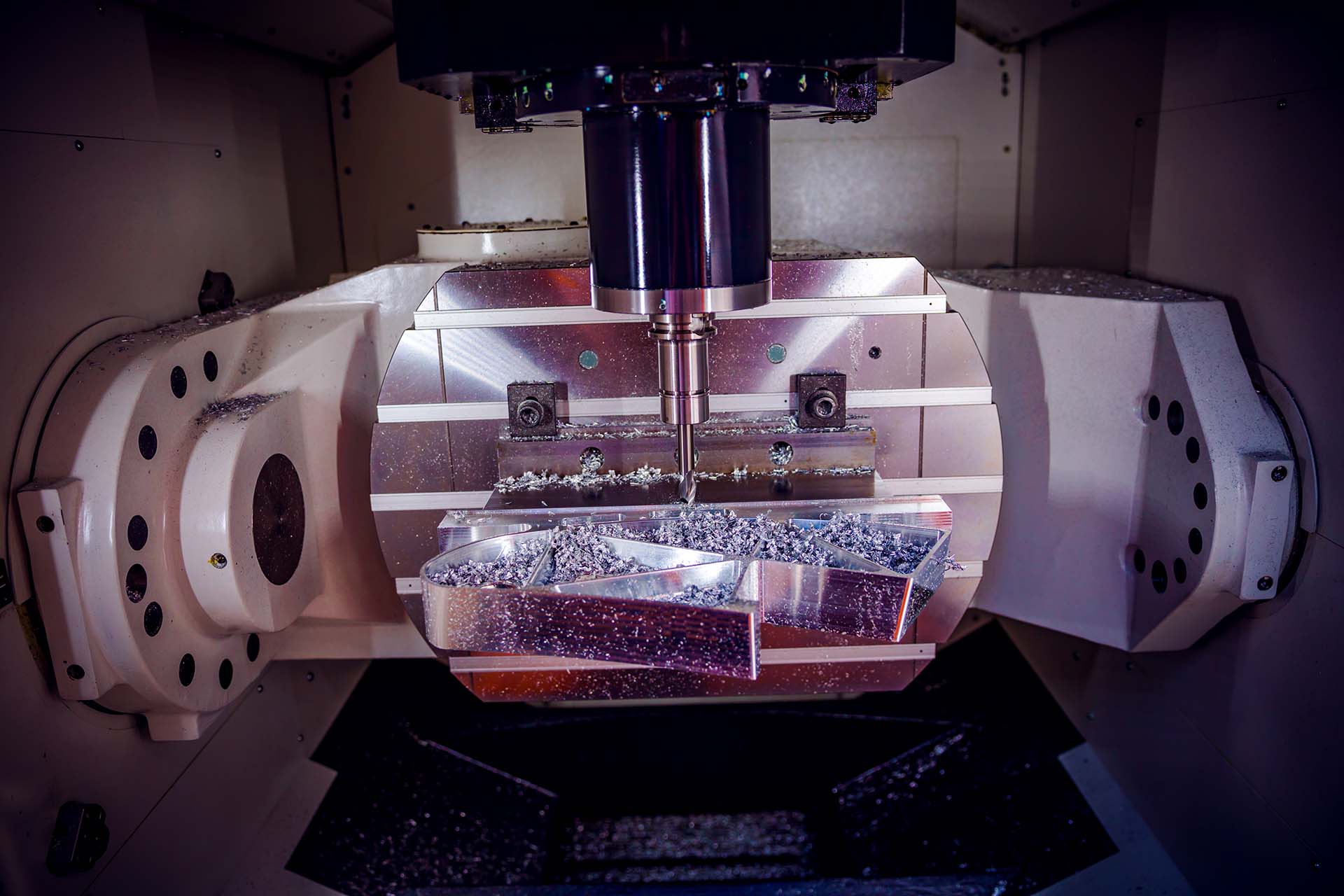
Precision Engineering
At our cutting-edge facility, we leverage advanced technologies such as EDM (Electrical Discharge Machining) and wire erosion to achieve intricate shapes and fine details with unmatched precision and accuracy. Our multi-axis milling capabilities allow us to produce complex components with tight tolerances and superior surface finishes, while turning processes ensure optimal precision for cylindrical components.
In addition to machining capabilities, we offer advanced laser welding services for joining dissimilar materials and achieving precise welds in challenging applications. Our expertise extends to the design and manufacture of jigs and fixtures, essential tools for ensuring accuracy and repeatability in any manufacturing processes.
Whether you require prototyping, small-batch production, or high-volume manufacturing, our team of skilled engineers and technicians is committed to delivering excellence at every stage of the process.
Partner with us for your precision engineering needs and experience the difference that our commitment to quality, innovation, and precision can make. Contact our Key Precision division to learn more about our capabilities and how we can help bring your vision to reality with precision-engineered solutions tailored to your unique requirements.
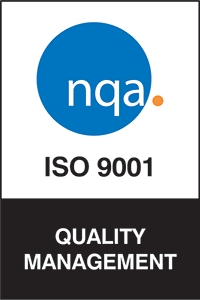
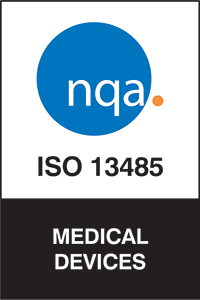
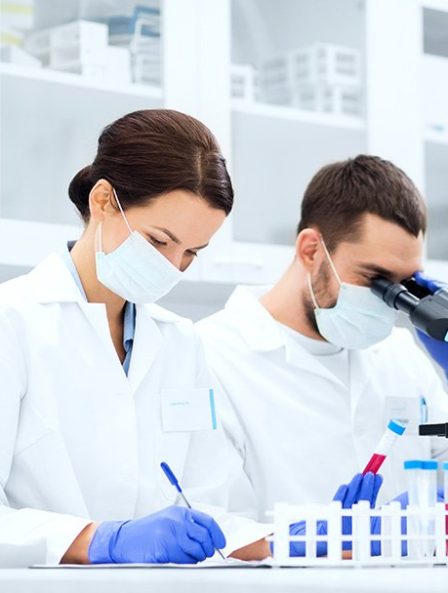
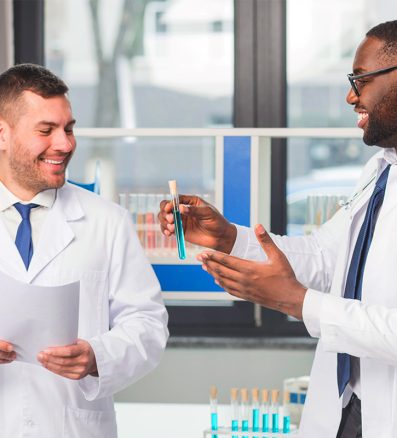
Injection Moulding
12 x Krauss Maffei 50T to 80T
5 x Krauss Maffei 110T to 350T
2 x Negri Bossi 830T & 850T
1 x Fanuc 80T
Certified Class 7 Cleanroom
Sepro Robotics /Full beam & Pick and Place
Processing 20+ Polymer types
Quality Lab with CMM measurement
Dedicated Assembly Room
Some Key Data
Years in Business
Million parts in 2023
Employees
Countries we Work with
m2 Facility
Key staff
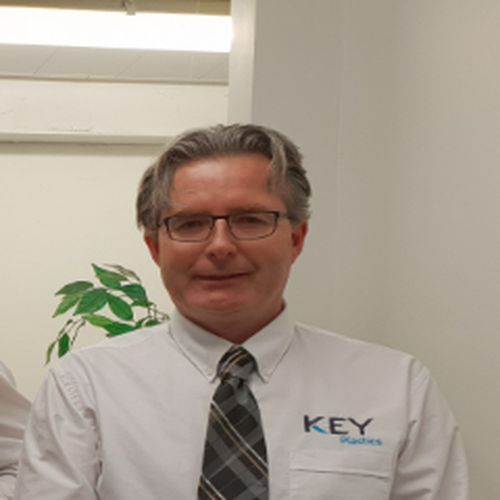
Managing Director
Eamonn Downes
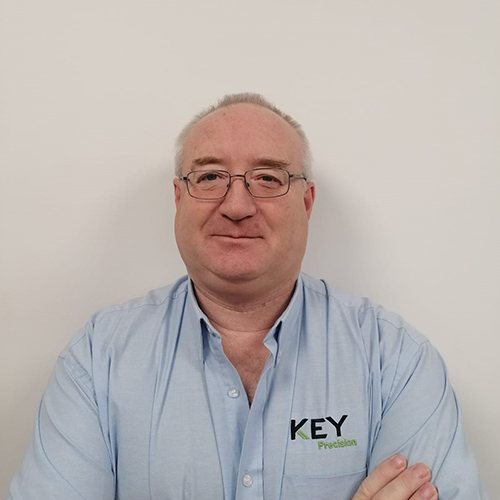
Engineering Director
Ciaran Downes
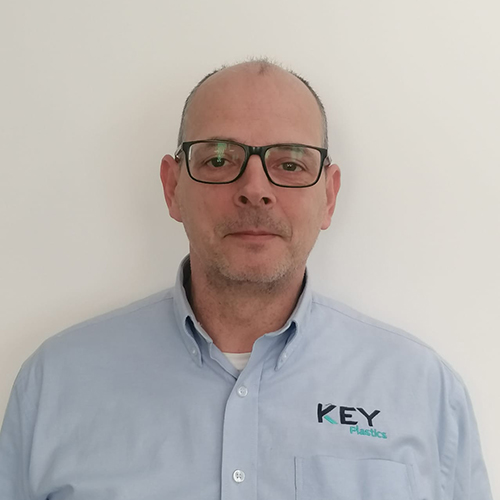
Moulding Director
Patrick Kearney
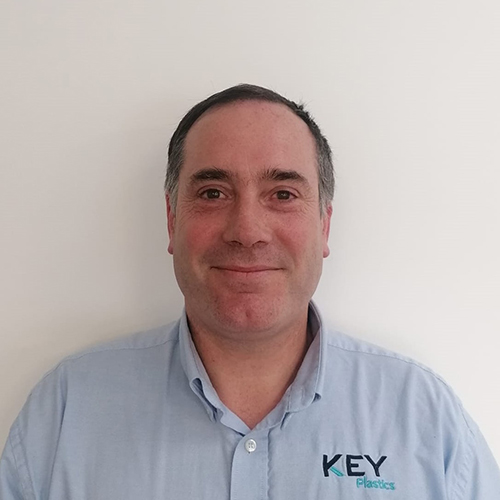
Business Development Manager
Jean-Marie Bocquel
Key Customers
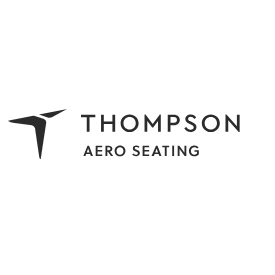
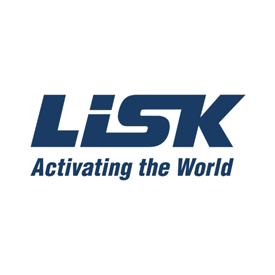
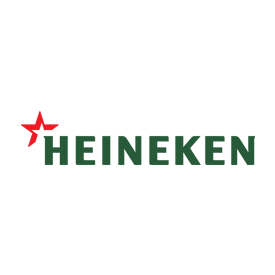
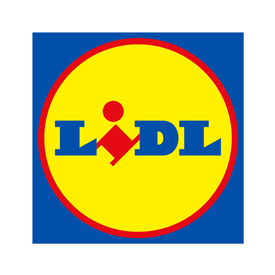
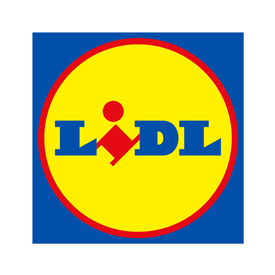
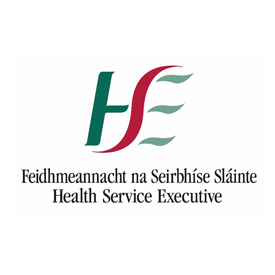
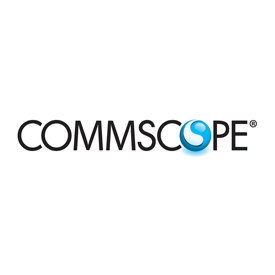
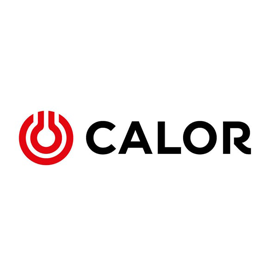
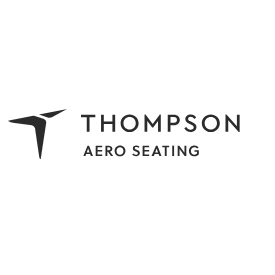
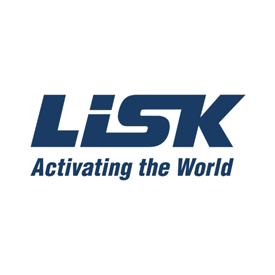
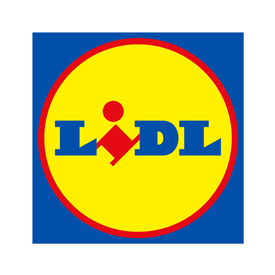
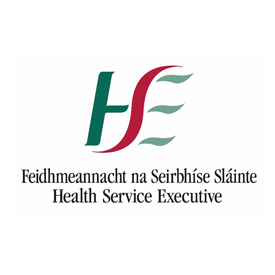
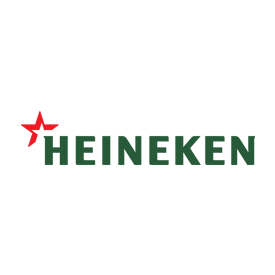
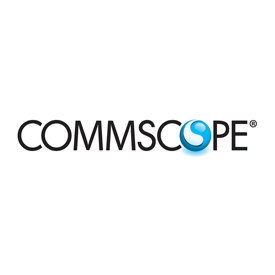
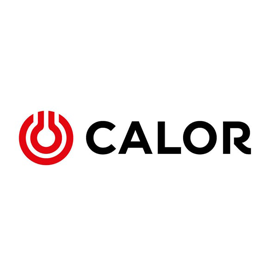